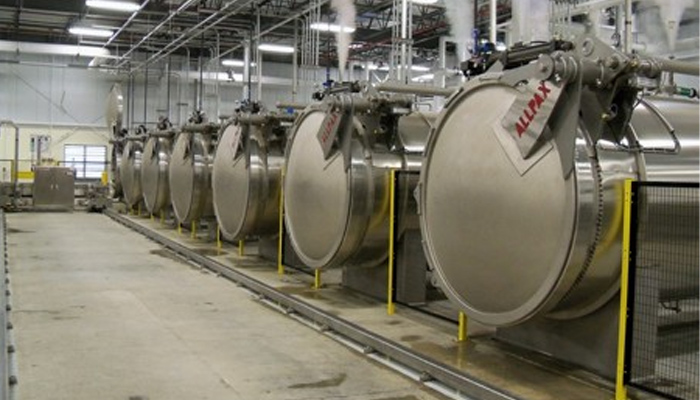
By Greg Jacob, Vice President and General Manager, Allpax
Serious challenges converge on today’s canneries. They face the ongoing evolution of containers, increasingly stringent food safety legislation and regulatory compliance initiatives, and emphasis on water usage reduction combined with the need to reduce operating expenses, improve efficiency, and increase capacity in existing footprints.
While the average life of a retort is 20 years, with some remaining in use for as long as 50 years, canneries can benefit from incremental improvements – making only those capital investments that make the most sense given the unique environment of the business. Instead of facing the daunting process of a complete upgrade, the cannery makes smaller investments in such areas as dual mode batch processing, food safety improvement through control upgrade, energy and water conservation that lead to reduced costs, and
retort room automation that frees up labor for more value added work. These improvements can pave the way for facilities to extend the life of the cannery with highly efficient and cost effective investments. There are four areas to consider when looking for incremental improvements that support future proofing a retort room.
Batch processing advances – dual mode retorts
Many canneries only process cans, yet pouches, trays, and other flexible containers are the up and coming package of choice for shelf-stable brands. A good future proofing strategy would be to upgrade to dual mode retorts – retorts that can process both cans and pouches today or have the hooks built in to easily and cost effectively add pouches at some time in the future. Many design options allow the cannery to purchase a retort with a migration path to dual mode or to purchase a completely outfitted dual mode retort. The cannery can look at the investment numbers and make a decision based on business projections. Dual mode is one of the most exciting areas for extending cannery life because it is so cost effective and versatile.
Using dual-mode retorts gives facilities the ability to use saturated steam for can processing or water spray overpressure processing for flexible or semi-rigid containers. A bank of retorts can be fed from multiple filling/container lines. Operators simply select the desired mode. No change parts are required to switch between modes. Since these retorts have a 1.8-meter diameter and six-basket capacity, they can process large quantities of product.
Control upgrades
While the longevity of retorts means companies have gotten a great deal of use from their initial investment, the problem remains that effective life of the retort vessel far exceeds retort controls. Retrofitting new controls is an excellent way to extend the life of the retort room, improve product throughput and quality, and meet food safety guidelines. New hardware and software controls bring new levels of technical support – SoildWorks 3D drawings and maintenance schedules right from the interface screen – and the latest in remote system monitoring that can shorten downtime from days to minutes.
Unlike manual operations where an operator is responsible for accurately documenting the process, today’s controls provide automated record keeping, eliminating human error inherent in manual documentation. An automated control system relies on PLC control with very tight tolerances on the process parameters, provides precise recipe management, and generates a report that is USDA/FDA approved (Title 21 CFR Part 11) and becomes part of the record.
In facilities using automated control, deviations automatically drop because the possibility for human error has been eliminated. By removing that risk, canneries have the assurance that product quality will not be jeopardized and brand names will not be damaged by a recall. In addition, operating costs are reduced because one operator can now manage an entire bank of retorts.
Additional safety advances through basket tracking
One of the biggest risks of a manually controlled retort room is the possibility that an operator will forget to turn the retort process on or accidentally move a raw basket to the unload side and bypass the retorts. As a result, there is a risk that raw product could go to market.
Basket tracking gives canneries the ability to track the basket through the system. There are now systems, including the Allpax positional ALLTRACK logic, that track the path of each basket. The ALLTRACK system for example relies on 2D bar code laser etched tags that are read by a self-contained vision sensor using pattern recognition software. Each Ethernet-based vision sensor has a stand-alone Internet protocol address for independent operation.
When an empty basket enters the first vision sensor zone, a number and personality are assigned in the ALLTRACK software. The basket personality includes the number of containers, production code, basket status (i.e. unprocessed deviation, uncleared deviation, etc.), the retort number, batch number, and other information. When the basket reaches its final destination, the last vision sensor confirms the basket number. If all parameters are met, the product is unloaded and sent to packaging. In between the vision system check points, each basket movement is tracked via discrete basket sensors at every location with a colored coded HMI display identifying each basket number and its dynamic status.
Sustainability advances
In a saturated steam process, a significant amount of vented steam goes into the atmosphere. By installing a state-of-the-art heat recovery system, vented steam can be used to create free hot water for cleaning and for heating food or other processes at a facility. In addition to vented steam recapture, water recovery systems for the retort cooling cycles can reduce water usage by as much as 50% and create free hot water for the plant to use in daily operations. Energy conservation systems rely on the latest control technology. It is not enough to merely capture and reuse the steam and water, the process must conform to food safety and retort operational guidelines. Partner with a vendor that has proved its competence with previously installed systems. The economic and social rationale for conserving energy and water will grow more important over time. Conservation options are definitely something to put on the investment radar.
Benefits of future proofing
Investing in benefit-rich retort and material handling upgrade solutions enables canneries to position themselves to optimize their current performance as well leverage their assets in the future. With the flexibility to adapt quickly to various types of containers, including standard metal cans and glass jars, to value-added polymeric and composite pouches, bowls, cups, and trays, these companies ensure their ongoing growth and economic success.
With the advances in batch processing technology, food safety, energy conservation, and automation, existing retort installations can implement upgrades while minimizing their capital equipment costs. Vertical retort users can achieve dramatic cost savings as well as enhance the quality of their operations by upgrading their controls without the need to install new retorts. Additionally, with the improvements in automated material handling, horizontal dual mode retort installations can reduce operating expenses, improve efficiency, increase capacity in existing footprints, and justify the capital investment.
For more information, please contact us or visit www.allpax.com