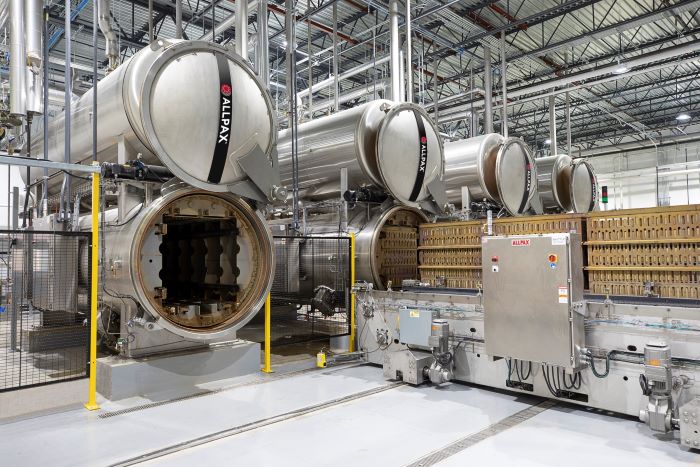
The Water Immersion Process is the most widely accepted method of sterilizing product using an overpressure process. The Water Immersion process is similar to a saturated steam process in that the product is totally isolated from any influence of cooling air – the product is totally submerged in water. But, it is different from Saturated Steam in that air can be introduced into the vessel during sterilization. Overpressure is provided by introducing air (or steam) on top of the water. In some instances, air is added to the steam (which then heats the air). The heated air agitates the water as it flows to the surface and serves to pressurize the process load.
Note on Terminology
In the Allpax retort control system there is terminology for an Uncleared Deviation or a (Cleared) Deviation condition that may exist. These terms are referred to in this paper. The definitions of these terms are as follows:
- CLEARED DEVIATION – When a deviation occurs, it may be possible to correct the process by adding time and/or temperature in order to compensate for the deviation. If this correction can take place in the retort, then the batch is declared to have a Cleared Deviation status. The Cleared Deviation status notifies the retort operator that a deviation was detected, but that corrective action was taken to compensate for the deviation (see Scheduled Process / Alternate Process definition). As in all cases, release of the product is subject to final review by the plant’s Quality Manager or Process Authority.
- UNCLEARED DEVIATION – When a deviation occurs in which an unsafe product condition exists and cannot be corrected for, then the batch is declared to have an Uncleared Deviation status. The Uncleared Deviation status notifies the retort operator that a deviation was detected and continues to exist in the batch.
Process Steps
Batch retorts execute a series of programmed process steps (also known as segments). These steps must be properly executed to achieve a sterilization process that meets the regulatory requirements imposed for food safety.
In a Water Immersion process these steps are:
- Prepare Tank
- Come Up Fill (A Sterilization Step)
- Come Up (A Sterilization Step)
- Cook (A Sterilization Step)
- Pressure Cool Fill
- Pressure Cool
- Atmospheric Cool
- Drain
Click the above image to see am animation of the Rotary Water Immersion Process
The following is a detailed description of each step:
PREPARE TANK – WATER IMMERSION
The purpose of the Prepare Tank step is to heat (superheat) the water in the Storage Vessel – the hot water reservoir. The Temperature, pressure and level are all brought to recipe-defined set points to complete the step. It should be noted that the door must be detected as closed and locked, along with the door safety detected as engaged before the step can be exited to the first come-up step.
In addition, to the water level, pressure and temperature checks performed in the storage vessel, and the door safety check performed on the Process Vessel, an I.T. check is also performed. This process step will not be exited until the water temperature in the storage vessel is greater than the product initial temperature entered by the operator.
COME UP / FILL – WATER IMMERSION
Also known as Vent Process Vessel or Sterilization I, the purpose of this step is to drop the superheated water that is stored in the upper vessel (the Storage Vessel) onto the product in the lower vessel (the Process Vessel.) In making this drop, the superheated water flashes in the process vessel and creates a saturating condition, forcing much of the air to exit (normally out of the Pressure Relief valve). For production retorts, the lower connection valve is opened until the level reaches the Preset Vent Completed Mark, at which time, the lower connection valve and the Pressure Relief valve is closed and the upper connection valve is opened to continue filling the machine. In addition, with the upper connection valve open and the Pressure Relief closed, pressure is controlled using the pressure control capabilities in the Storage Vessel, for both the Storage and Process Vessel.
The exiting of this step is dependent on the upper level mark in the Process Vessel being attained (the level sufficient to cover the baskets). In some machines, this is a digital probe level indicator.
COME UP – WATER IMMERSION
Also known as Sterilization II, during this step, the pump remains on, and the rotation continues (if a rotary process), and the temperature and pressure continue to be controlled to the set point. In order to successfully complete and exit this step, time and temperature conditions established in the recipe (this should be in accordance with the filed process) must be met simultaneously. At the end of the scheduled come-up time, the retort must be at, or above, scheduled cook temperature (unless there are multiple come-up steps) to prevent an Uncleared Deviation during the Cook step. If these conditions are not met, the phase time may be extended so that the process exit condition can be reached, without creating a deviation. Flow, level and rpm conditions (if a rotary process) are monitored. If flow, level or rpm’s fall outside of the acceptable range at any time during the step, an Uncleared Deviation Condition is created.
COOK / HOLD / STERILIZATION – WATER IMMERSION
Also known as Sterilization III, the Cook Step involves sterilizing the product after it has reached the established Cook Temperature throughout the retort (the purpose of the Come Up step). In order to successfully complete and exit this phase, the conditions established in the recipe (this should be in accordance with the filed process) must be met for the length of the process. Throughout the scheduled cook time, the retort must be at, or above, scheduled cook temperature, at or above water level for the entire length of the cook – a predetermined level sufficient to cover the top of the basket, the flow must be within an acceptable range for the entire length of the cook, and at acceptable RPM speeds (if rotary process). If the temperature condition is not met, and an alternate process is available to the controller, a Deviation condition is created and the cook time may be extended by the alternate. If no alternate is available, then an Uncleared Deviation condition is created.
Flow, level and rpm conditions (if a rotary process) continue and are monitored. If flow, level or rpm’s fall outside of the acceptable range at any time during the step, an Uncleared Deviation Condition is created. If an Uncleared Deviation condition exists at the end of the scheduled time, the process step can be exited only by an operator override.
During this step, the operator is required to make operator entries: at least one check and entry of the MIG reading, one for the Chart reading, and one for the Sight Glass Level check. All operator entries must be made for the step to be completed. Should the sight glass Level check indicate a failure (water is visibly below the level needed to cover the product basket in the Process vessel), then an Uncleared Deviation condition would be created.
PRESSURE COOL / FILL – WATER IMMERSION
This step begins the cooling process, while simultaneously filling the Storage Vessel. Cooling water enters the Process Vessel, while the upper connection valve (that connects the top vessel to the bottom vessel) is opened. The cooling water entering the process vessel forces the warmer water through the connection valve into the storage vessel. When the storage vessel is filled to the recapture level, the step ends. Note: Circulation (Flow) and RPM’s (if a rotary process) continue.
PRESSURE COOL – WATER IMMERSION
This step continues the cooling process in the Process Vessel. Cooling water enters the Process Vessel and flows through the Pressure Relief valve (then exits the retort), which controls pressure. When the pressure cool time is completed and an established temperature setpoint in the Process Vessel is achieved, (both conditions are met,) the step ends. Note: Circulation (Flow) and Rpm’s (if a rotary process) continue.
ATMOSPHERIC COOL – WATER IMMERSION
This step continues the cooling process in the Process Vessel. Cooling water continues to flow into the Process Vessel and flows through the Pressure Relief valve, which has been fully opened, releasing pressure (note: this pressure may be steadily released using ramp control by ramping pressure in a separate Pressure Cool Step). When the atmospheric cool time is completed, and an established temperature setpoint in the Process Vessel is achieved, the step ends. Note: Circulation (Flow) and RPM’s (if a rotary process) continue.
DRAIN – WATER IMMERSION
This step drains the water from the retort. The drain is opened the water gravity-drains from the retort. When the level condition is met, the step ends. Note: To accelerate the drain step, limited overriding air pressure (2-5 psi) may be used during the step.
A complete line of retort room equipment, including water immersion (rotary) retorts, is available from Allpax Products.