A Brief Overview
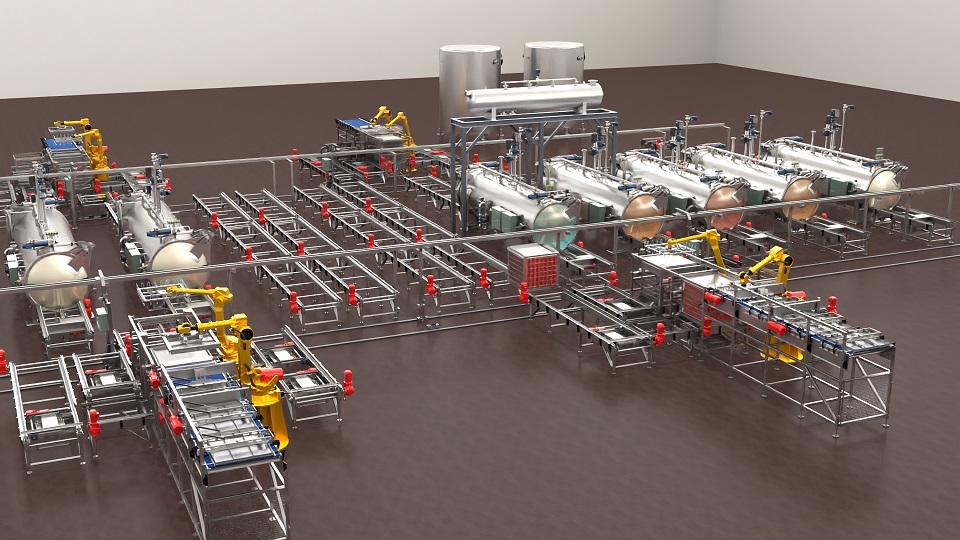
One of the many considerations to be addressed when designing and equipping an Automated Batch Retort System (ABRS) is how to convey the product filled containers through the line.
Product Handling Equipment (Loaders & Unloaders)
First of all, the multitude of containers that are available to food manufacturers today require different types of container handling equipment to facilitate the required production levels needed to operate a profitable line. Here are some examples of the different types of container loading and unloading systems that are available today:
Rigid containers such as steel or aluminum cans and glass bottles or jars are typically loaded into and unloaded from baskets with sweep-type loaders and unloaders. In these machines, unprocessed sealed containers from the capper or seamer are received, accumulated, and formed into a layer pattern. A basket is moved into position and a layer of containers is swept into position at the top of the basket. Divider sheets are placed in between the layers and this process is repeated until the basket is full. The opposite process occurs in the unloader, and containers are discharged in mass, one layer at a time, and eventually combined into a single lane to meet downstream packaging equipment needs.
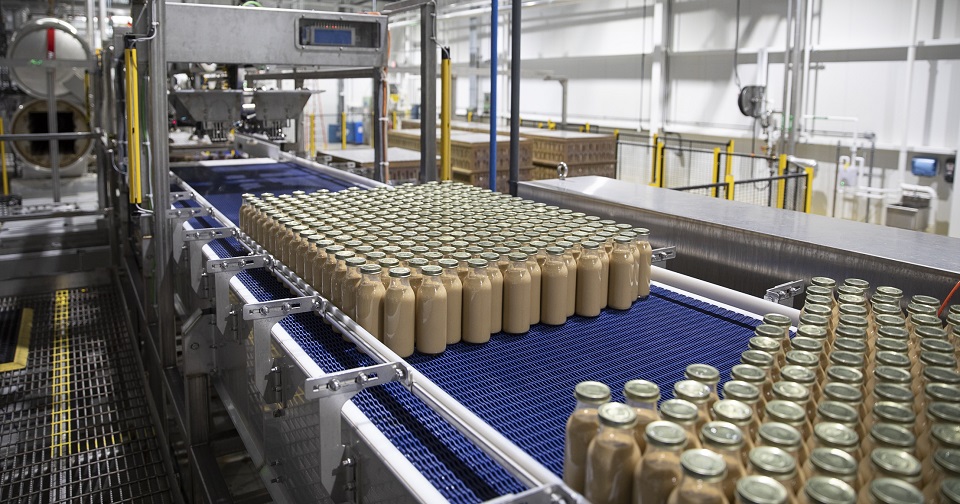
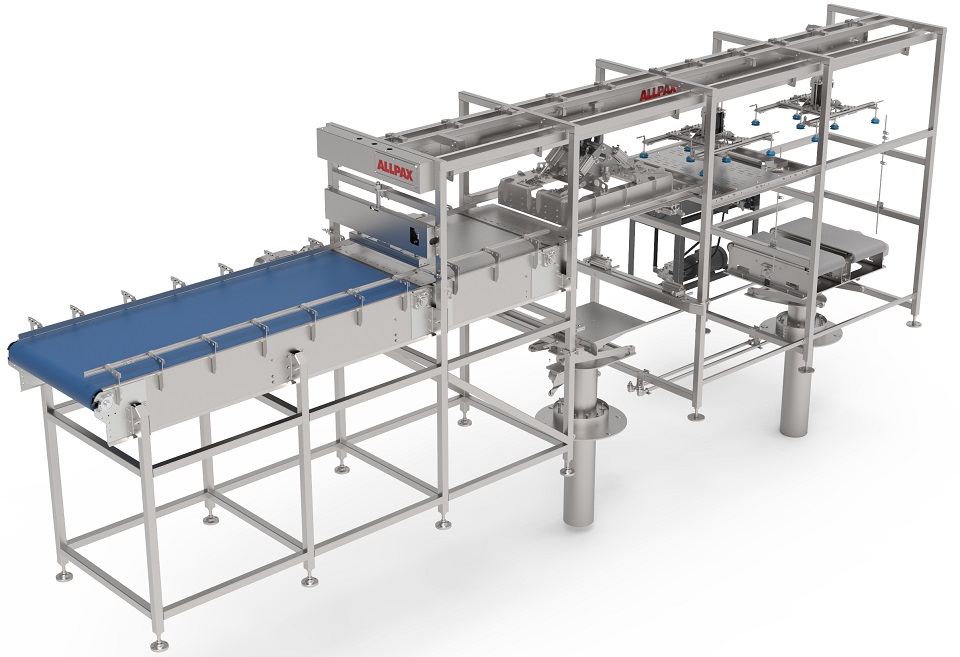
Semi-rigid and flexible containers such as pouches and thermoformed bowls, tubs, trays and bottles are handled differently because the containers cannot support the weight of the layers above. These applications require self-stacking and supporting trays, and containers are picked and placed into and off of these trays with either gantry style or multi-axis robotic type loaders and unloaders.
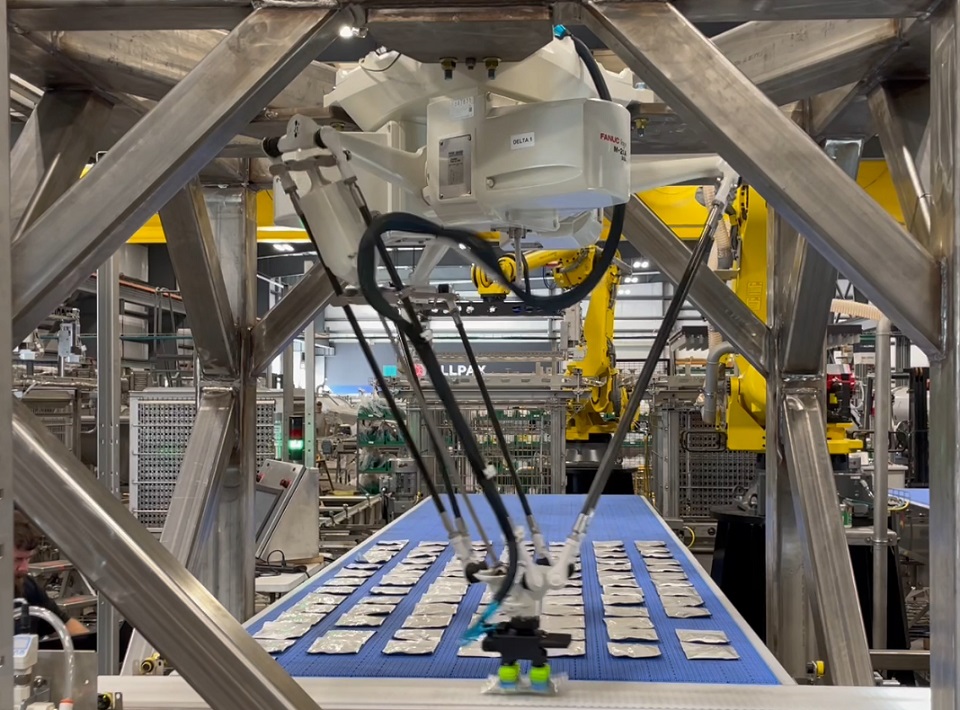
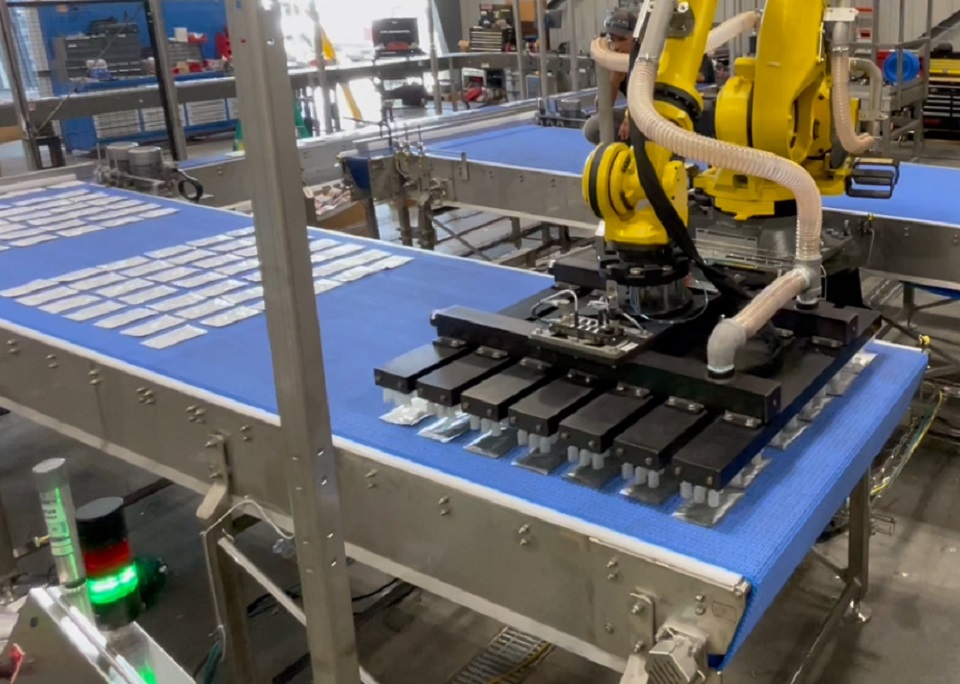
A third type of loading and unloading system that is designed for handling plastic bottles is the fragile container loader/unloader. This system consists of unique sweep-type loading and unloading equipment that forms and pushes rows of bottles into and out of specialized trays that are indexed up and down within a basket frame.
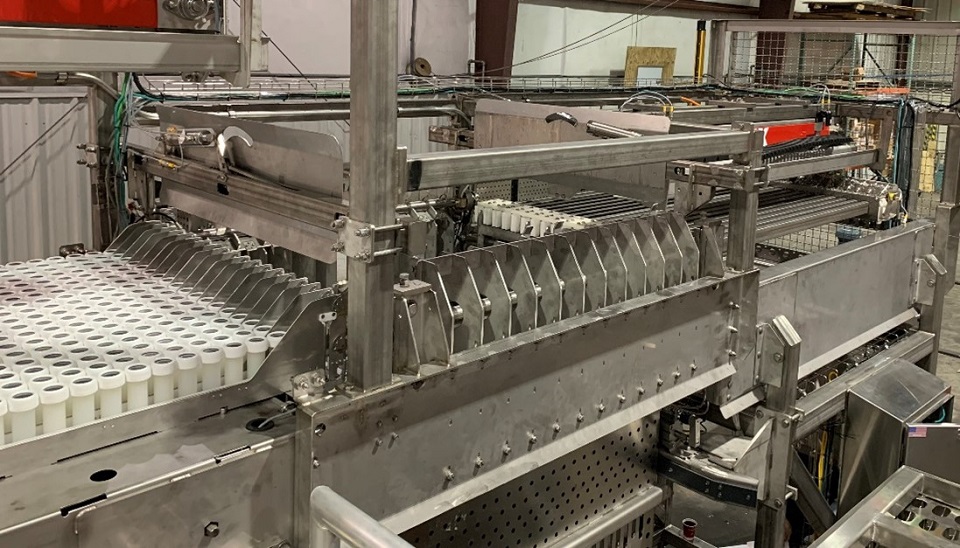
For more budget-minded applications, there are also various basket and tray material handling systems with less automated function than the above-mentioned product loading and unloading equipment. Below are 4 examples of degrees of automation available for basket loading and unloading applications (i.e.: for rigid containers).
Basic Lift Stations elevate the basket contents to the rim so the product can be manually swept by operators into or from the basket via a conveyor system. Placement or removal of divider sheets in between container layers is manually done by the operator. Carts/baskets are manually moved to and from the loading and unloading stations and the retort(s) by operators.
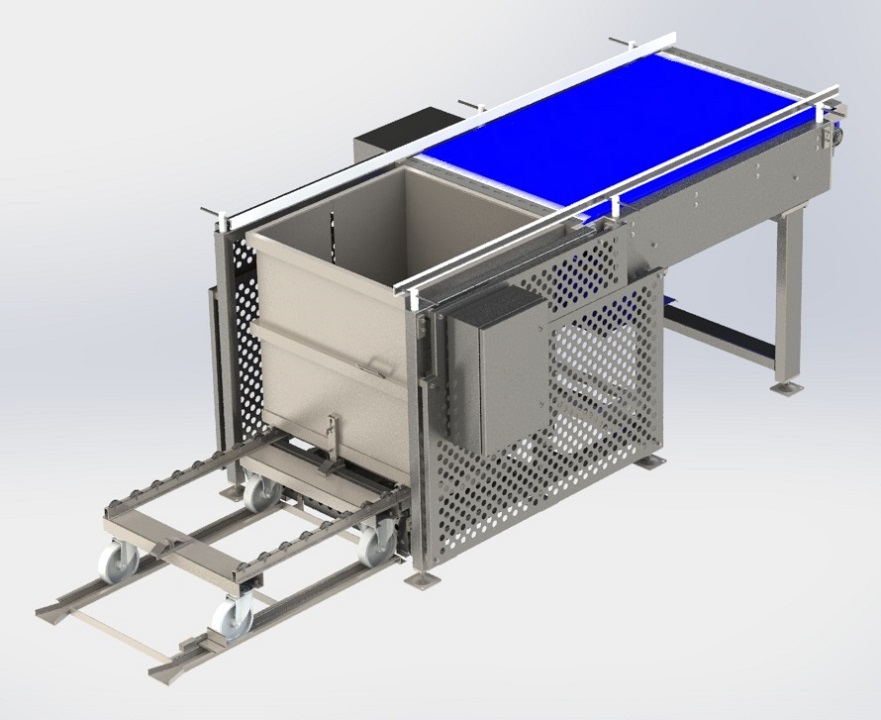
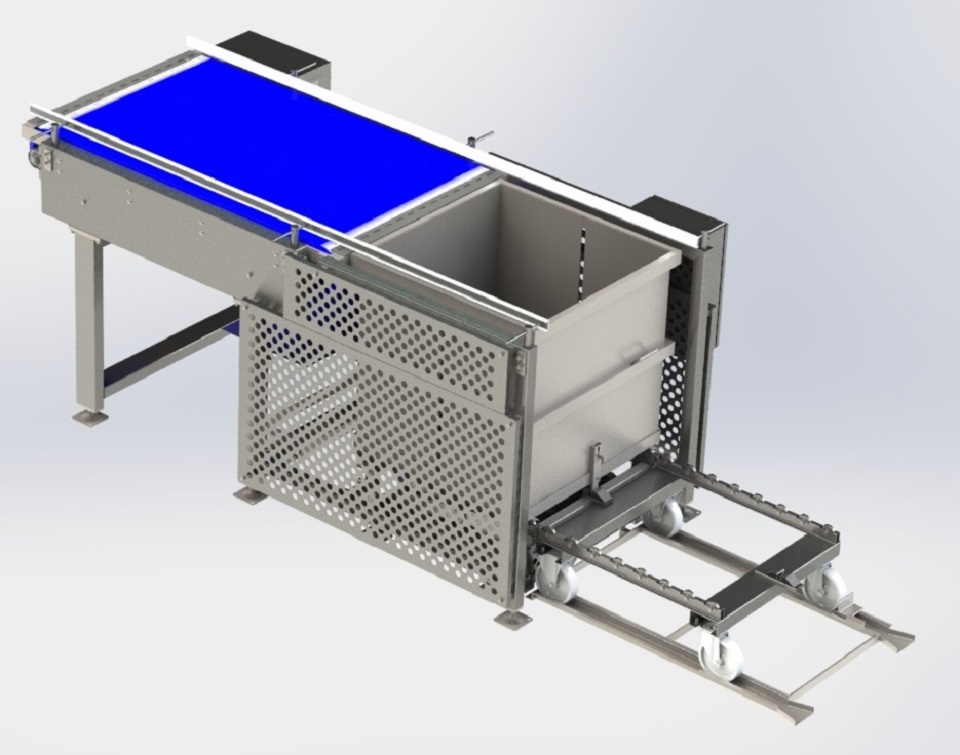
Moving up in level of automation, a mechanized sweep head is added to sweep an entire layer of containers into or out of position at the top of the basket. Operators manually add and remove the divider sheets between layers, and manually transport and position baskets/carts into and out of the loader and unloader.
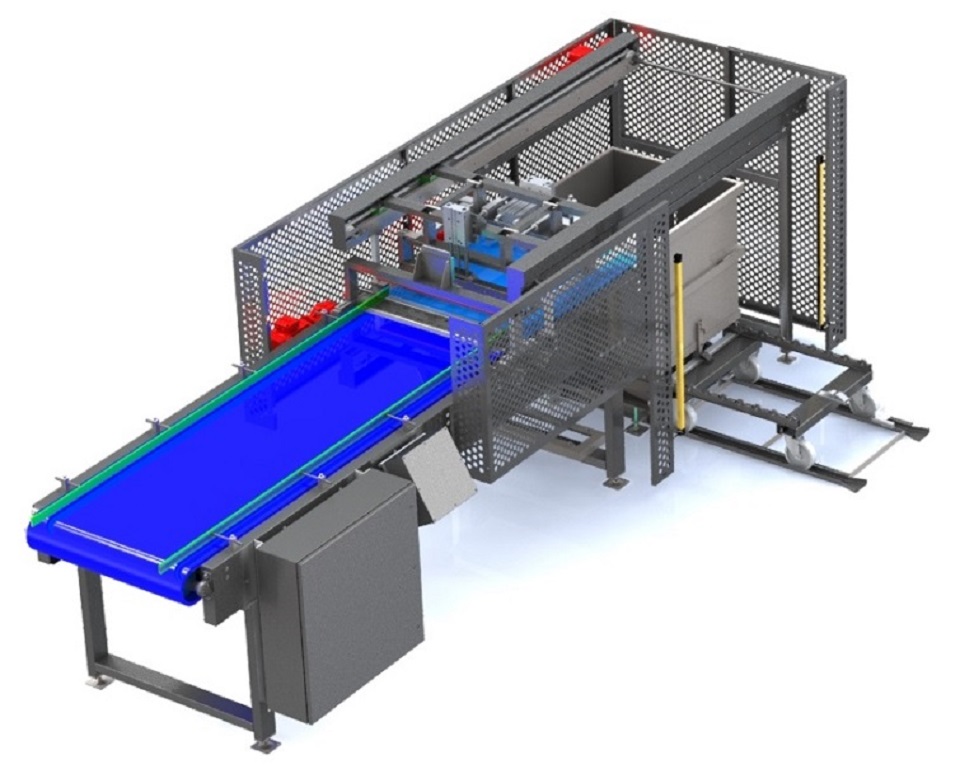
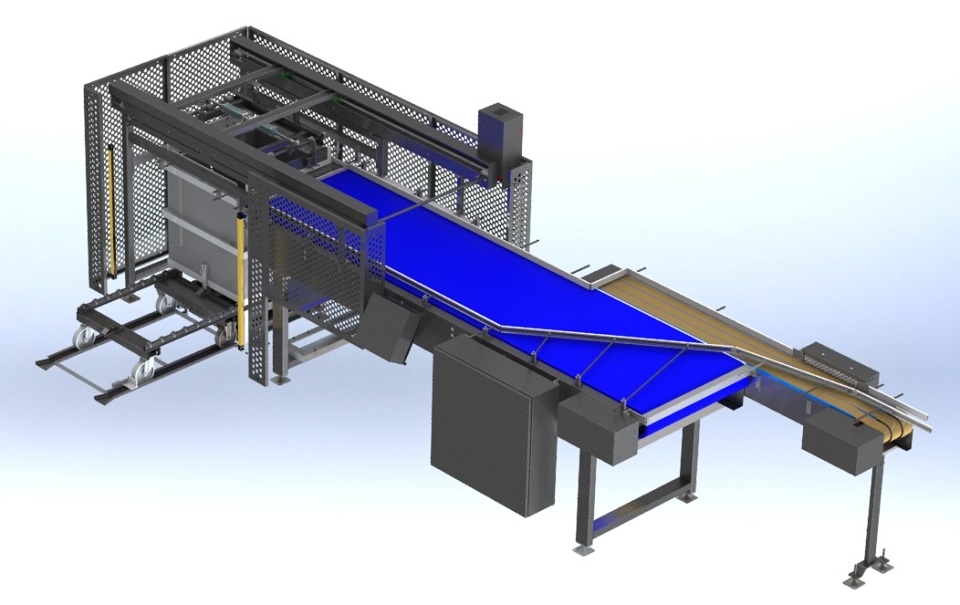
The next level of automation adds the function of picking and placing the divider sheets into and removing them from the basket after the layer of containers has been swept into or out of the baskets. Baskets/carts are still moved/positioned by the operator.
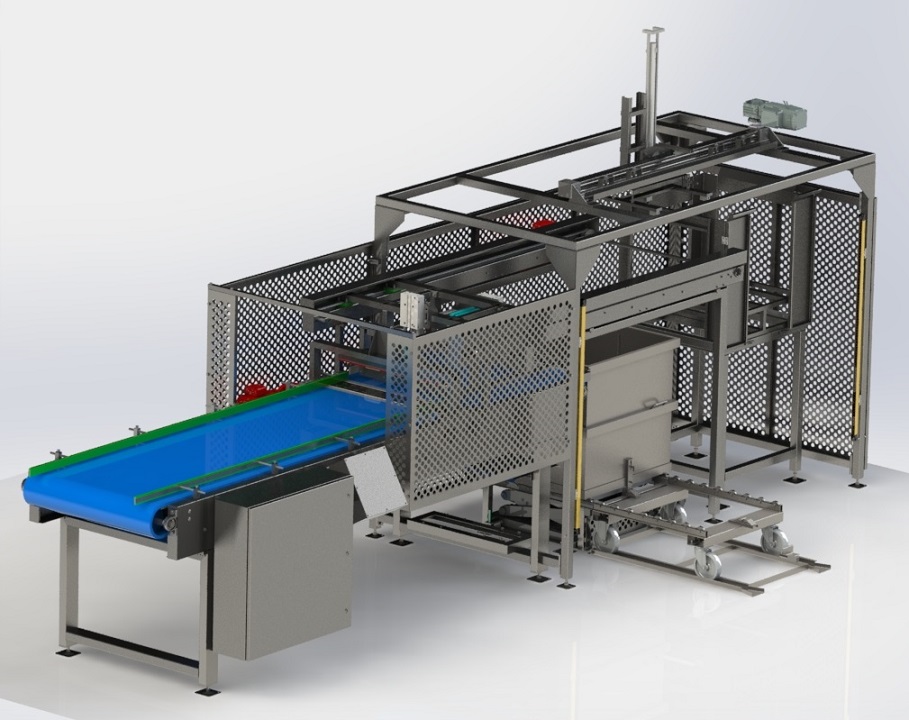
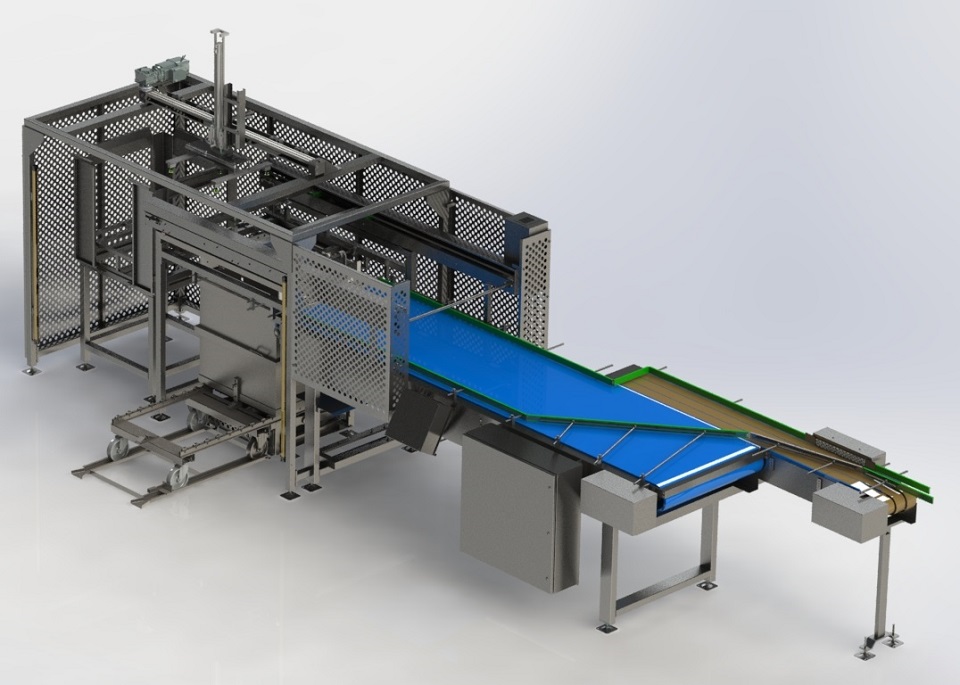
Lastly, there are systems performing all basket loading and unloading functions including sweeping product into and from the basket, placing and removing divider sheets, and conveyance of product baskets and divider sheets from the unloader to the loader. This system requires only one two operators. Moving loaded baskets from the loader to the retort and from the retort to the unloader remains the task of the floor operator(s)
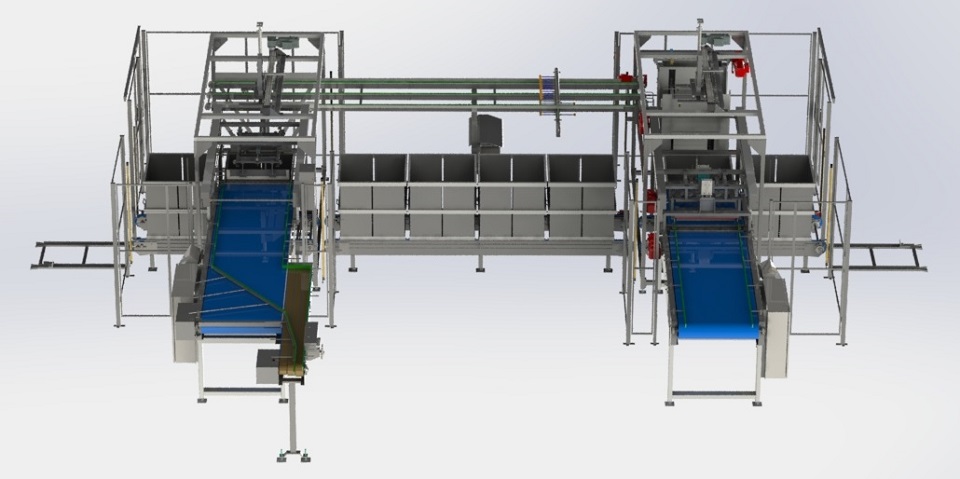
Retort Delivery Equipment
The second major material handling component of an ABRS involves delivery the of product from the loading area to the retort(s) and then from the retort(s) to the unloading area, otherwise known as the retort delivery system. Here too, varying degrees of automation can be considered, from manual to fully automated systems. Depending on how the retort room is laid out, there are several options for accomplishing automatic conveyance of products/containers to and from the retorts.
Basket or tray stack conveyors are typically used in situations where the available floor space is minimal and/or there are obstacles in between the loader/unloader area and the retorts. Other items that are typically part of the basket conveyor system include the following.
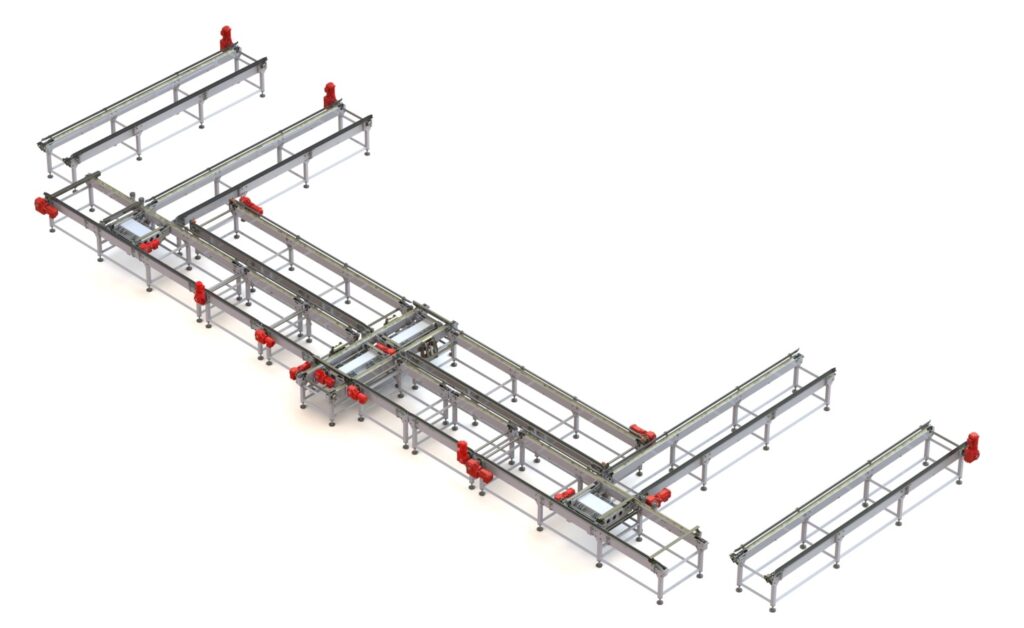
Tippers are used to shed excess water from the tops of the containers before they are delivered to the unloader.
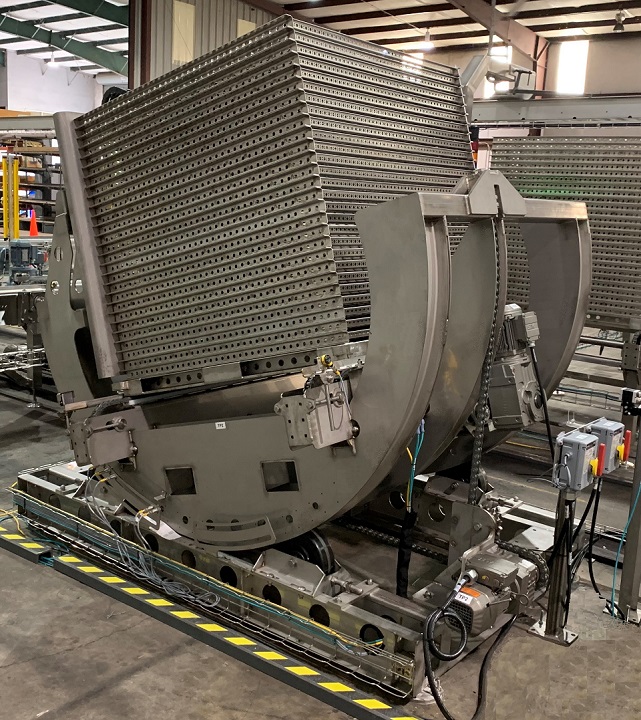
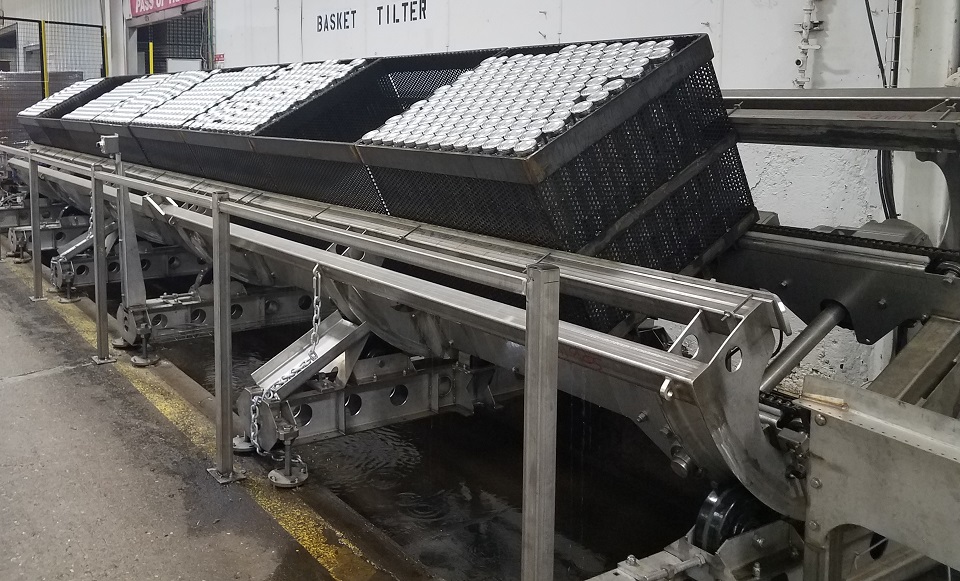
Pop-ups allow 90° direction changes and turntables can perform the same function while also changing the orientation of the baskets or tray stacks by 90°.
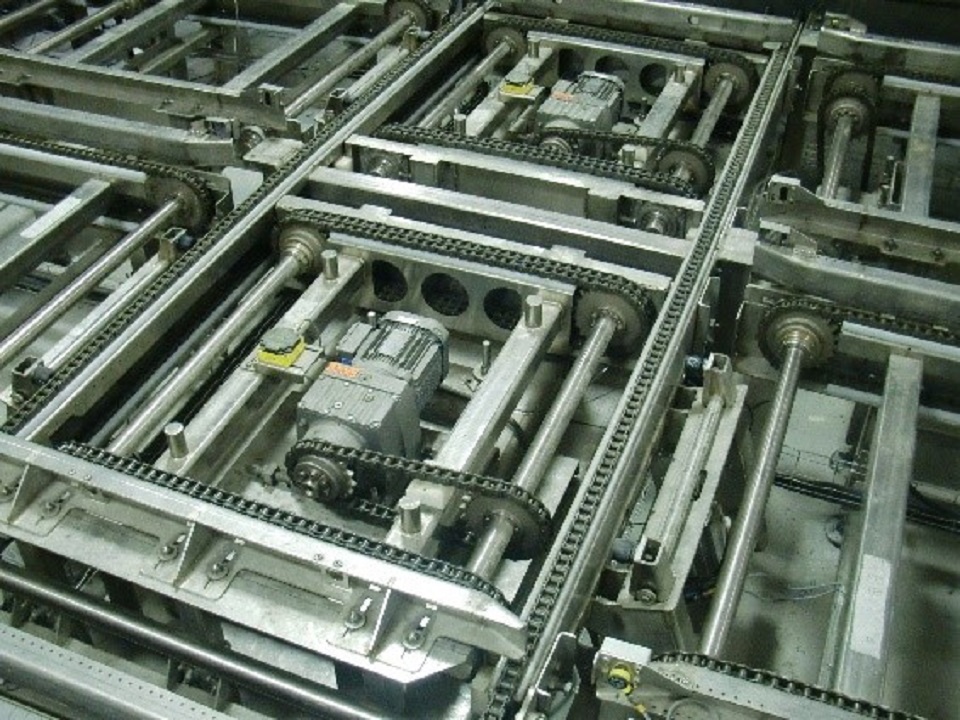

Shuttles are typically used when there is unobstructed space between the container loading and unloading area(s) and the retorts. These are highly efficient retort delivery systems that can be used to transport complete or partial retort loads and can even load and unload two retorts in one trip. Shuttles can also be equipped with on-board systems to push and pull loads of product into and out of the retort, respectively, thus eliminating the need to have a chain conveying system installed in the retort which must withstand the harsh environment. Various shuttle designs are available that can carry 1 to 8 baskets or trays stacks at a time. Below are some examples of the various types used in Automated Batch Retorts Systems:
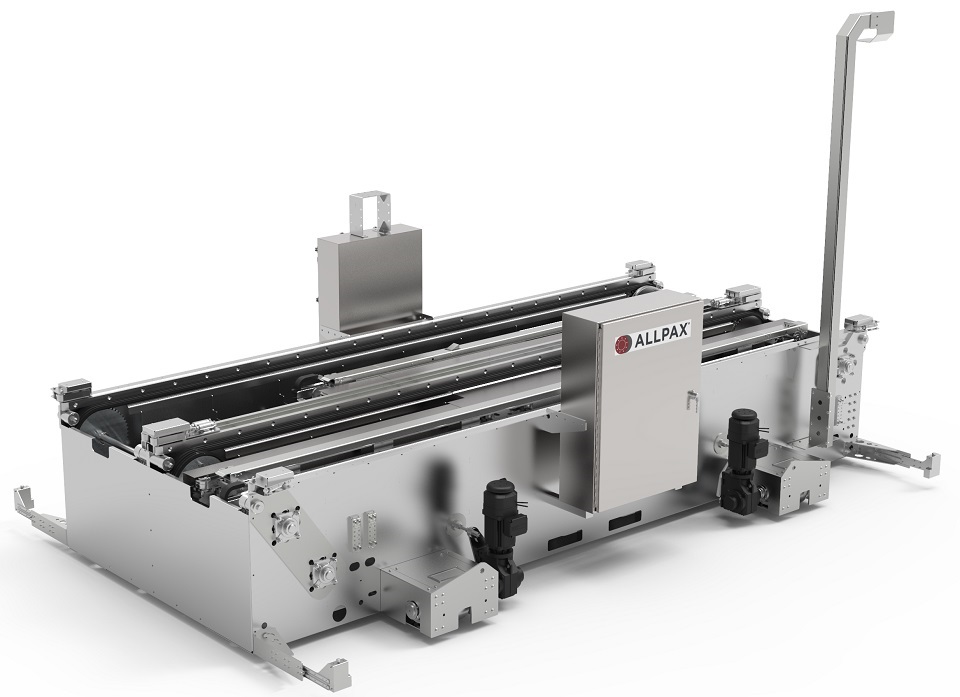
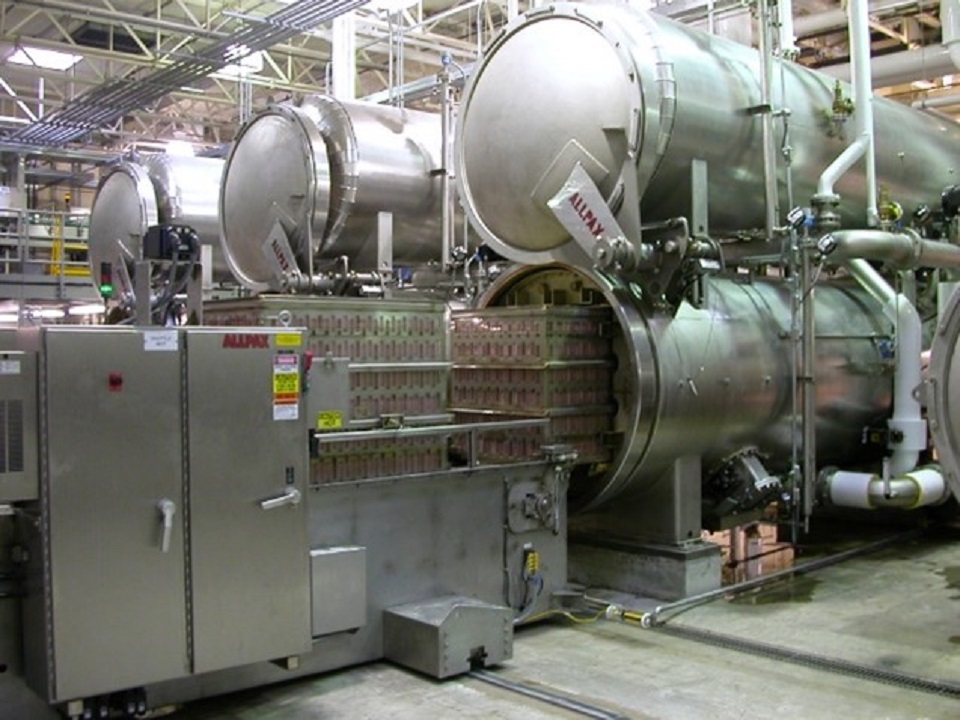
High speed shuttles are utilized when floor space is a constraint, and the length of the shuttle must be minimized. Their increased traverse speeds allow for higher throughput capability in the retort room. These shuttles typically hold 1 to 2 baskets/tray stacks at a time.
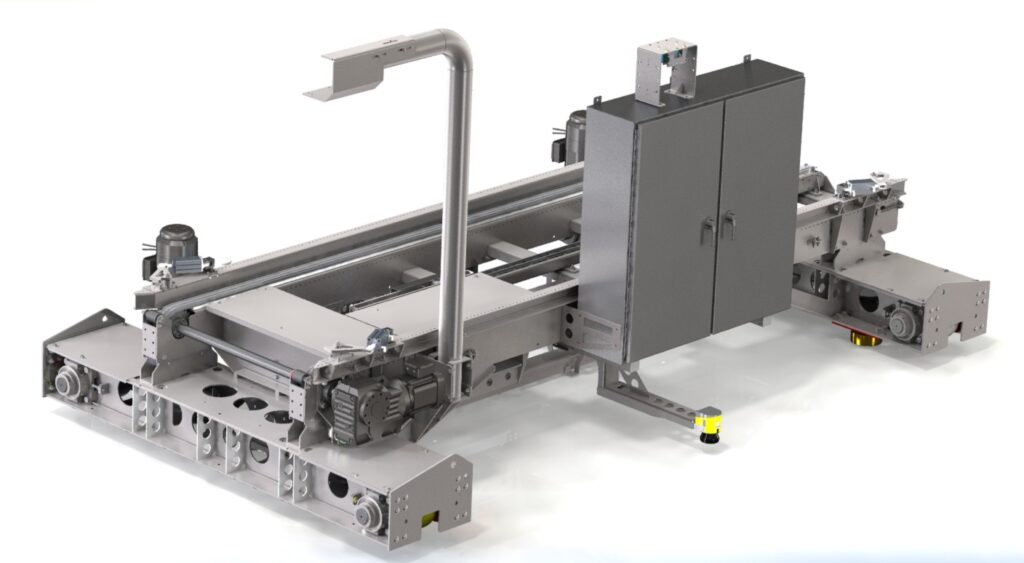
Automated Guided Vehicles are typically used where there might be obstacles and/or the path between the loading and unloading area(s) and retorts are not straightforward. Because these types of vehicles are typically limited to the size and weight of load they can carry, multiple vehicles are required. Consideration of product mandate times and retort cycle duration must be made to accommodate the greater amount of time it takes to transport loads between the retorts and the loading/unloading area.
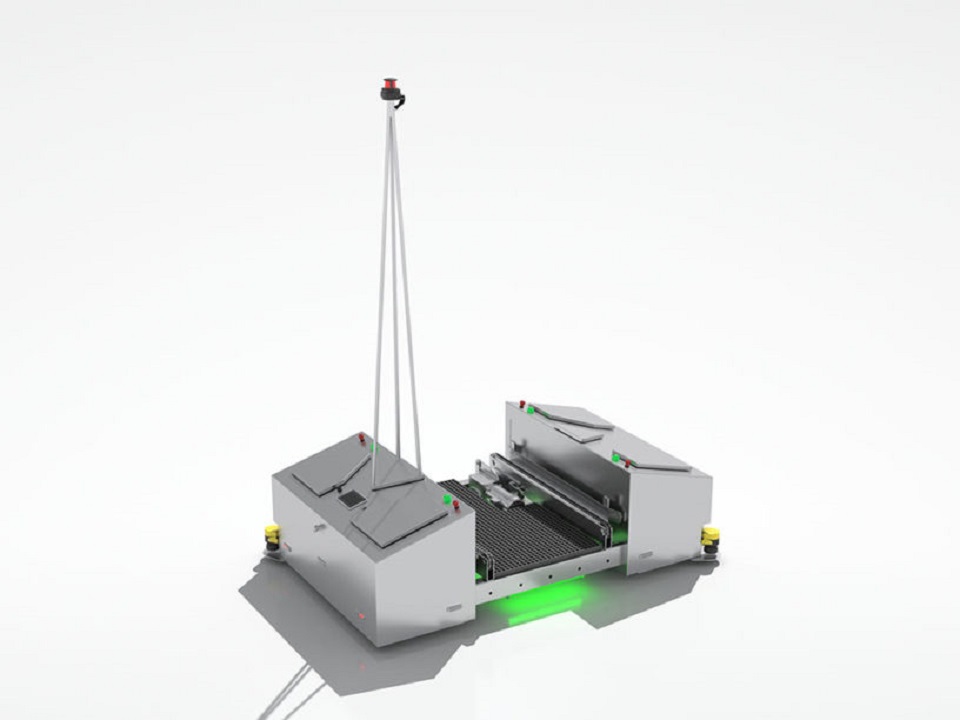
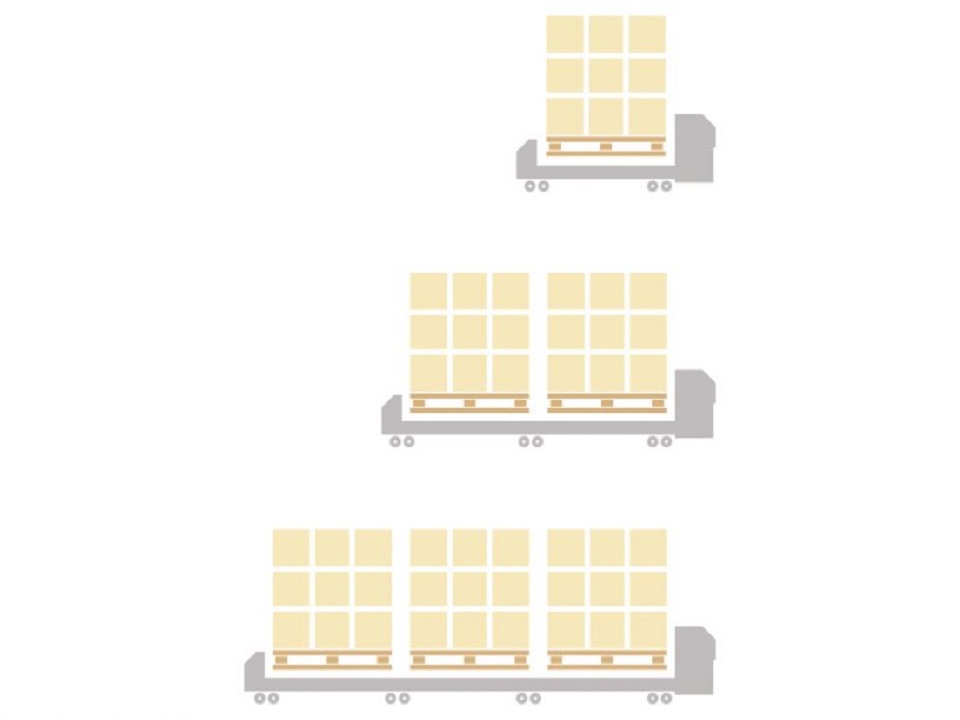
Other available types of retort delivery solutions to allow for the insertion and removal of product into and out of the retorts in a more automated or mechanized fashion include retort mounted internal conveyers, and Rigid Chain Loaders/Unloaders. These devices help to reduce the risk of moving heavy product baskets and tray stacks into and out of the retort.
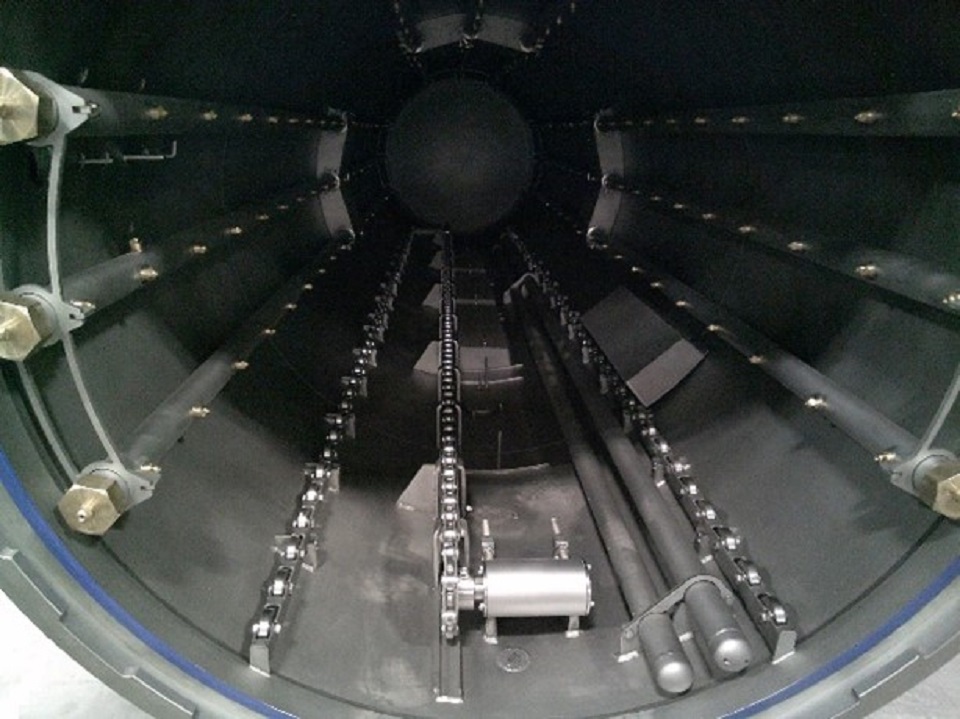

When budgetary constraints limit the expenditure on material handling equipment in the retort room, there are still options for the food manufacturer. Ergo Loaders/Unloaders are used to load and unload retorts when baskets and tray stacks are transported on carts or by fork trucks to and from the retort manually by human operators. Ergo Loaders/Unloaders, as the name implies, reduce the risk of injury from inserting and removing heavy loads into and out of the retort.
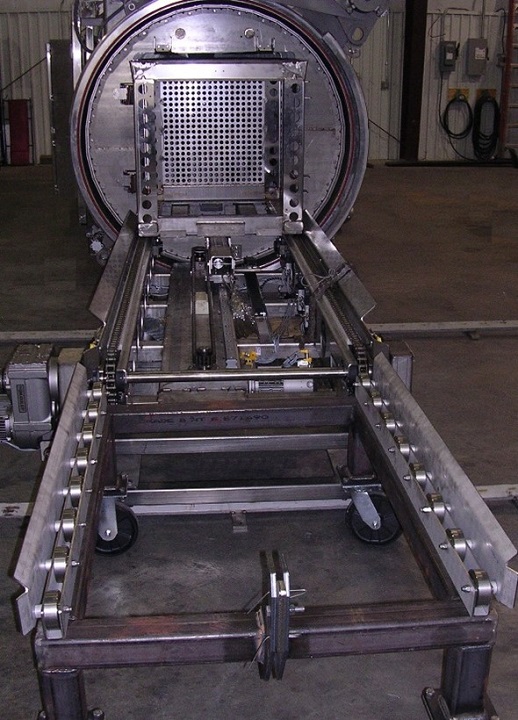
It should be noted that when the retort diameter is above 1400mm/54”, baskets laden with product can become quite heavy. In such applications, some type of retort delivery system is highly recommended to reduce the risk of injury to retort room operators. While the above-mentioned systems can add considerable upfront investment cost to a retort operation, they also provide for lower labor costs and reduce operational risk from a product and personnel safety standpoint. In high volume production lines, automation systems can provide significant returns on investment.