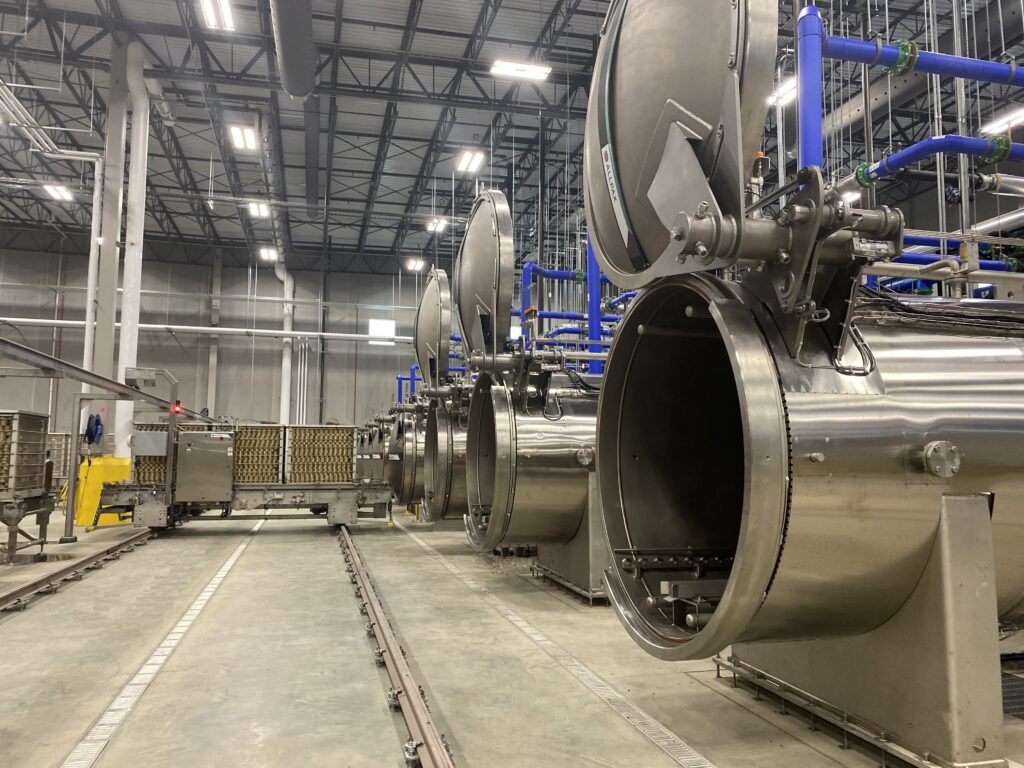
A Note To Plant Engineers & Employees re: 21 CFR Part 113
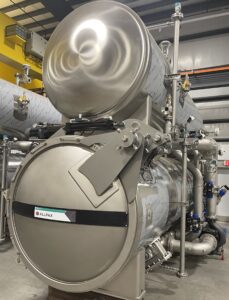
Engineers are people that make things happen in the plant. When the line is down, it is the engineer or maintenance manager that gets the phone call. It is the engineer that must get involved in the fix. When the line needs to increase its efficiency, the engineer is the person who designs the change.
In maintaining, changing or upgrading food processing equipment, it is important for engineers and maintenance managers to recognize that retorts are a special breed of machine. Retorts must be given special consideration in the decision process when replacement parts or upgrades are being considered. A common mistake that many engineers (particularly those that come into the industry with little, or no food background) make, is that the regulatory agencies are primarily concerned with issues related to plant and machine sanitation or quality issues regarding grading.
However, food processing regulatory issues go far beyond the scope of a clean plant. Food safety is THE primary concern. And, when it comes to food safety, there is no area that gets more attention than the retort room. There are published regulations that address the retort, the design, and the conditions under which these retort designs are operated. In the retort room, the primary concern of the regulatory agencies is that the retorted food product has been given a sterilization process sufficient to eliminate the type of food spoilage which would cause a health hazard to the consumer.
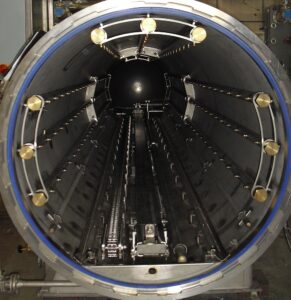
The mechanisms involved in assuring that the retort adequately sterilizes the food product can be quite complex. Retort manufacturers implement designs which assure that every retort that is manufactured meets or exceeds the requirements of the regulations. Bleeder requirements, flow calculations, steam quantity, steam header pressure and container orientation comprise just some of the critical factors that we use to design retorts. Good process control software and controls should also be an integral component of the retort, with software designs that assure that the retort meets the controllable process parameters – the parameters that are critical to proper sterilization for the product.
Retorts should be validated at the time of installation to confirm the retort design. In addition, the retort control system should be challenged to validate that it will deliver and appropriate process schedule that is adequate to produce a sterile product. When completed, this validated unit – complete with its complement of component parts, valves and instrumentation – stands as an integrated system that has met the challenges.
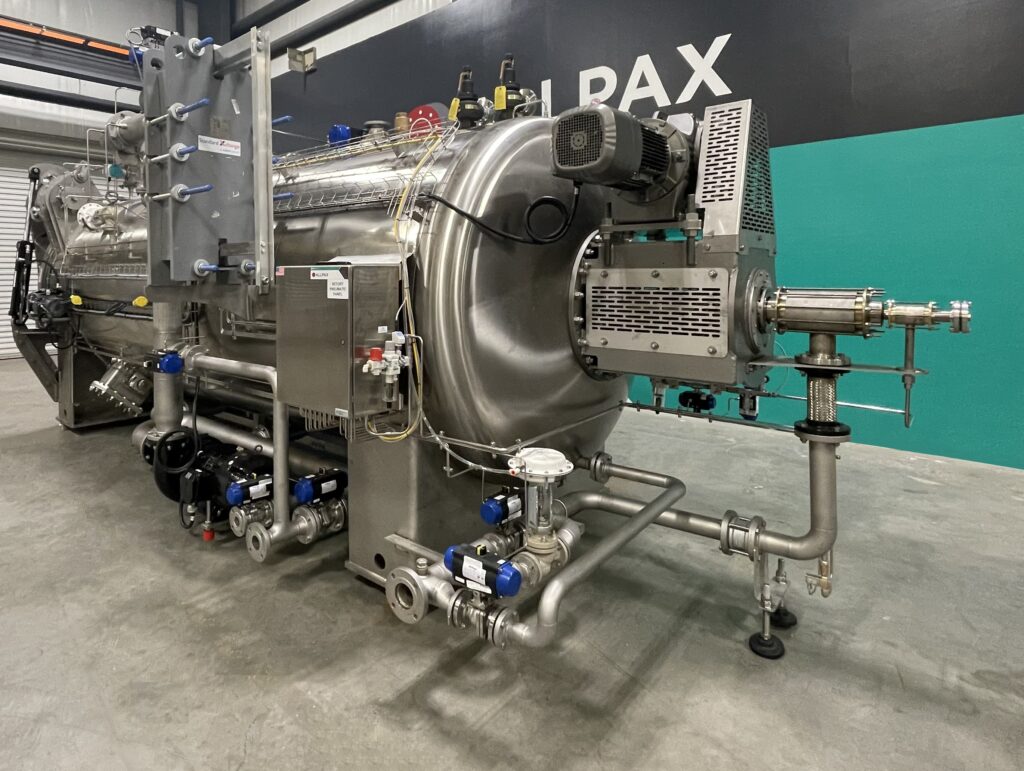
One serious concern of the regulatory agencies is that of the well-intentioned engineer, who, in trying to improve process efficiency or save energy, makes design or process modifications to retort equipment. These modifications, which may accomplish energy-savings or efficiency goals, may serve to defeat the ability of the retort to properly sterilize the food product.
The regulatory folks see the validated retort (components, controls and software) as a complete entity. Once installed and validated, modifications cannot be made to the physical design of the retort, the control system logic affecting sterilization, or the process system, without performing the tests to re-validate the machine.
As an engineer involved with retorts and the retort room, it is in your best interest to become familiar with the government regulations regarding retort processing, and to understand how these regulations should affect your decision making, when it comes to retort system implementation and modifications. There are two documents that should be a ready reference for the engineer: