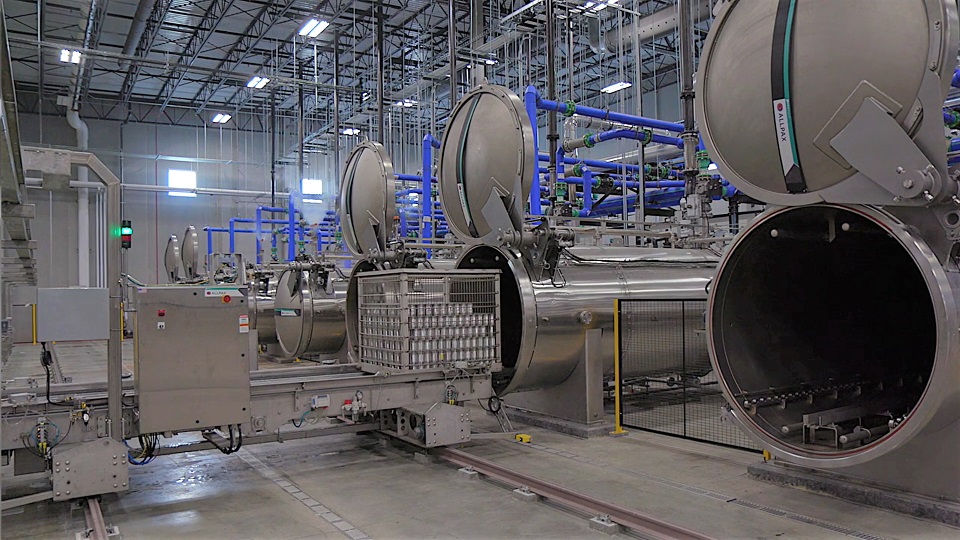
Companies that invest in revitalization do so to increase capacity, spur sales, lower risk, or decrease costs
Retorts have exceptionally long service lives and since the equipment in older canneries has been paid for many times over, when does it make sense to invest in new retorts and state-of-the-art control technology?
There are two primary and a number of secondary motivations – drivers – for revitalizing a cannery. These are:
Primary
- Product demand outstripping capacity
- Growing inability for co-packers to maintain and/or expand the customer base
Secondary
- Incidental factors such as energy, safety, labor costs, obsolesce, or compliance issues
If these drivers are absent, the cannery in all likelihood will continue with its installed base of aging equipment and long running processes. If the drivers are there, managers at older canneries will often opt for the advantages of revitalization, which include increased capacity, improved sales, lower business risk, and decreased operational costs, typically in reduced labor. Understanding these drivers and what they mean for the organization will go a long way toward making informed decisions on revitalization.
Capacity issues
Cannery management usually begins researching revitalization when capacity cannot support customer demand. Capacity shortfalls not only limit total sales, but also pose a competitive risk. For example, competitors can gain a foothold by filling the shortfall and what begins as an inability to meet demand can end up as a struggle to maintain market share.
Sales issues for co-packers
The customers of co-packers want a great price and also assured supply, high quality, demonstrable food safety, and overall low risk in doing business with the cannery. When given the choice between dealing with a cannery that utilizes equipment and processes that are more than 20 years old and dealing with a cannery that features newer equipment with state-of-the-art controls and superior FDA compliance, the newer cannery will win over the older cannery if their prices are roughly in the same ballpark.
There are several reasons why co-packer customers opt for new over old. The first is risk aversion. If a cannery looks outdated, then the customer could question how long it will be able to not only maintain production, but also to expand it. The second is the social bias toward adoption of the latest technology. Most people covet the newest cellphone or tablet computer, not a flip phone or desktop computer. Customers experience no perceived value in older technology. And it is not only a “perception thing.” Newer systems have controls that assure consistently safe food and document that fact.
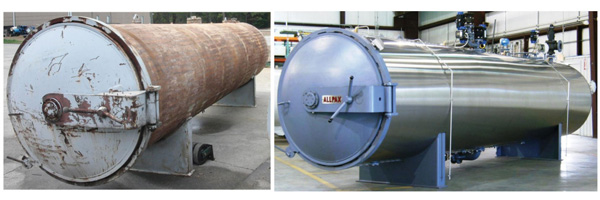
Labor, energy, water, and compliance
There are a number of secondary issues that can contribute to a full or partial makeover of a retort room, but these points generally are not prime factors in the decision to revitalize. These include:
- Labor cost
- Worker safety
- Energy and water consumption
- Process reporting that relies heavily on manual record keeping
- Maintenance issues with aging retorts and control systems
These secondary factors typically can lend weight to a decision to go ahead with a revitalization project. Or if there are extenuating circumstances as described later in this article, these considerations can lead to a partial upgrade. The following actual examples of primary and secondary drivers show what is possible when they are taken into consideration for a revitalization project.
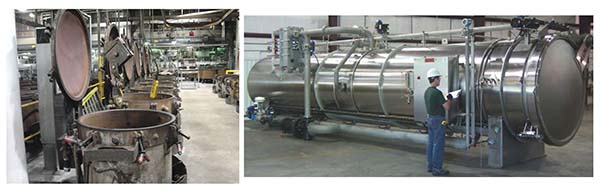
Capacity issues at a Midwestern cannery – a primary driver example
A Fortune 500 company with a name brand canned vegetable knew it could sell more if it had more cases of product to sell – a classic capacity issue. Because of this primary driver, management opted to completely replace all of the aging vertical retorts at its Midwestern facility in favor of a new fully automated retort room. The company also wanted an automated batch reporting system fully compliant with new FDA regulations. The plant’s production requirements could only be achieved, it was thought, through the addition of 1800 mm horizontal retorts commonly referred to as jumbo retorts due to their 1.8 meter diameter and six-basket capacity.
Like many revitalization projects, this wasn’t as simple as pulling out the old and putting in the new. The problem Allpax saw after an audit of the plant was that the retort room did not have the width to accommodate 10 side-by-side jumbo retorts – the number needed to meet the anticipated increase in capacity. Allpax personnel examined the available floor space in terms of width and length, taking into account the space required for an automated loading/unloading system.
The Allpax solution to the limited width in the room was to manufacture retorts eight baskets long, not six baskets long like standard jumbo retorts. The eight basket retorts would be 38 feet long, an extension of eight feet over the six basket retorts. Allpax’s overhead orbital retort doors open up, not out, and this would also help ensure that the retorts fit into the available space. The seven longer retorts could stand in place of the ten shorter units and meet capacity requirements. Three fewer retorts meant the cannery realized a 20 percent savings as compared to the cost of 10 machines.
In order to load and unload eight baskets of product in an efficient manner, Allpax also had to develop a shuttle system that was fast, yet small enough to fit in the available space. The supplied laser guided shuttle carries two baskets at a time and traverses across the floor at up to 275 feet per minute. The shuttle also has a built-in function to quickly link the baskets together as they are loaded into the retort, and de-link them during unloading. All of these features were new for this application. This novel approach decreases the loading and unloading time, while also providing the significant benefit of eliminating the need for a powered chain conveyor inside the retort.

New retorts process either cans or flexible packaging
The company asked Allpax whether it could develop dual-mode jumbo retorts that could process either cans or flexible packaging. This ability to process both types of packaging would give the company flexibility and the potential to lower future capital costs. Allpax has extensive experience in both technologies and designed the new jumbo retorts as dual mode; saturated steam for can processing or water spray overpressure processing for flexible containers. Operators can simply select the desired mode. There are no change parts required to switch between modes.
Allpax was responsible for providing the supervisory control and reporting software needed for retort operation and for generating reports that would be used for FDA reporting purposes. Allpax personnel also programmed the new fully automated retort room loading/unloading system, where filled and sealed cans are automatically loaded into baskets, transported to and loaded into the retorts, unloaded after the processing, and then transported back to the packaging line where they are labeled, packed into cases, and shipped. The system is also equipped with a complete Basket Tracking System that automatically tracks and documents every move of every basket within the system.
As designed by Allpax, the automated retort room — loading/unloading automation and seven jumbo retorts — can be managed by a single operator and this allows for a significant reduction in labor. For all of its programming needs, Allpax has a team of software engineers available 24/7 to log into a retort system via virtual private network and troubleshoot problems, providing any troubleshooting that the customer needs in real time.
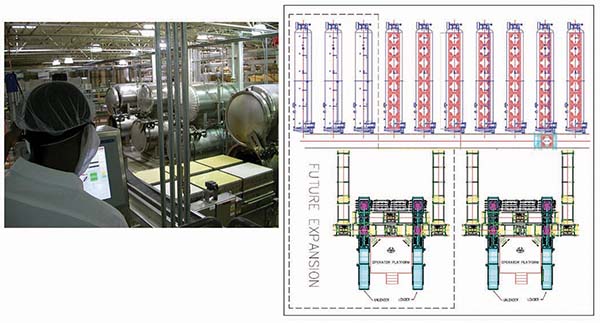
Plant capacity increased by more than 25 percent the first year the new jumbo retorts were in operation. Furthermore, lowering labor cost meant that the cost per retorted can went down and margins went up.
It is important to point out that with a revitalization, canneries gain the option of 24/7 instantaneous technical support via the Internet. This support tool can ease the transition from a last-generation to a new-generation cannery and also lower risk. Having a knowledgeable software or controls engineer virtually in the retort room via a private network reduces the anxiety that operators, maintenance personnel, and managers may feel when working with state-of-the-art-technology for the first time. It is certainly a cost effective support option and one that rapidly solves problems.
Customer base issues at a Southeastern cannery – a primary driver example
A meat canning co-packer in the Southeast serves private label accounts, club stores, brands, and foodservice operations. This company’s products are recognized for their quality. One of the company’s most important club-store customers toured the facility as part of a supplier evaluation program. The club store customer raised the following concerns with its co-packer.
- Capacity wasn’t sufficient for the customer’s growth objectives
- The advanced age of the retorts raised the risk of production slowdowns or shutdowns
- Antiquated controls raised food safety risks
The customer said that unless these issues were addressed, its business would be taken elsewhere – a classic example of the primary customer base driver for a co-packer.
Cannery management saw the threat of losing a strategic customer as only part of a bigger problem. Management not only wanted to satisfy this customer, but also to expand capacity so that the company had a wider base of customers. In other words, grow sales and reduce the exposure of too much reliance on a single mega customer.
To revitalize the cannery, the company relied on Allpax for an automated batch retort system with eight horizontal retorts and a state-of-the-art control system. The automated system reduces labor costs and runs multiple can sizes for greater flexibility. The new controls provide record keeping in accordance with regulations and consistent processing batch to batch. The club store customer rewarded the company for this investment with additional orders.
While the cannery continues to operate the older retorts, long-term plans call for a gradual revitalization of that section of the plant, including full automation. The present revitalization protected the current customer base while opening the door, through increased capacity and lower labor costs, to expand to a wider customer base.
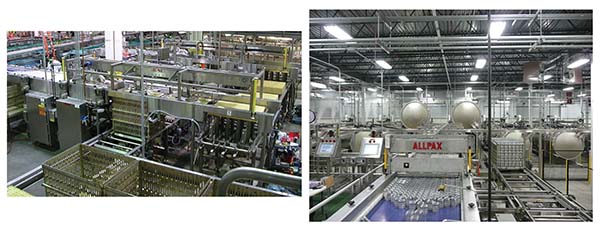
Secondary issue of obsolete control system spurs partial upgrade
An older brand owned vertical retort cannery in the Northeast is profitable and its production capacity is sufficient for demand. Management saw no need for revitalization. Both the aging retorts and control system required extensive ongoing maintenance, but the cost in labor and parts could easily be borne by revenue.
The status quo was put into jeopardy on the day a senior maintenance technician reported that he was retiring due to serious illness. It turned out that this technician was the only person in the cannery with the expertise to keep the obsolete retort control system operating. Compared to today’ systems, the controls were ancient. Replacement parts and general system know-how were virtually non-existent.
In consultation with Allpax, the cannery opted to replace the control system with state-of-the-art control technology. Today the company produces high quality canned goods in older vertical retorts. The system features off-the-shelf Allen-Bradley PLCs and Allpax monitoring software that exceeds the requirements of 21 CFR Part 11. The software suite offers a host of features designed to increase uptime, throughput, and food safety. There is a wealth of information and parts available to maintain the system and the controls will carry the cannery in good stead for years. This is a good example of a secondary driver opening the door to a partial revitalization.
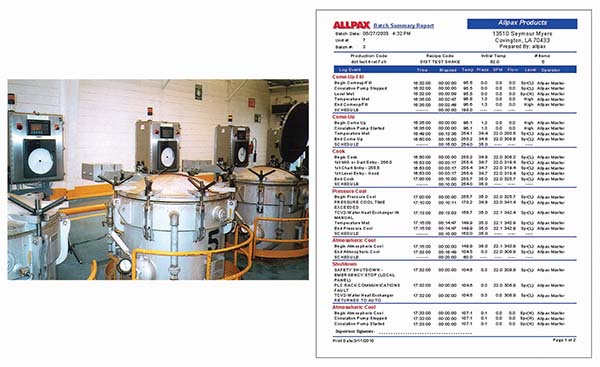
Canneries are often surprised and gratified to learn that controls upgrades can also be used to improve the overall safety within the vertical retort room. There are a number of PLC-based control strategies to ensure that operators do not manually open the door of any vessel that is pressurized beyond a safe level.
Secondary driver – energy and water – prompts waste heat recovery system
A large international brand, a leader in the many categories it competes in, initiated a corporate-wide effort to improve sustainability. Cannery management at a facility in the upper Midwest was charged with reducing waste and conserving energy and water at the plant as part of the overall corporate sustainability guidelines. This is a case of a secondary driver opening the door to a focused upgrade.
Allpax developed the technology for a system designed to lower energy costs and reduce water consumption on the company’s horizontal retorts. The FDA requires retorts to be purged of residual atmosphere before the shelf-stable process begins. In the “come-up vent-open” process, steam is flushed through the retort and vented out of the facility for a specified period of time. The Allpax waste-heat recovery system captures the “come-up vent-open” waste steam in a vented tank where the steam condensates into hot water of about 200˚ F.
This hot water can be used to supplement hot water in lavatories and cleaning stations or it can be run through heat exchangers for heating food or other processes at a facility.
In this instance the cannery decided that revitalization would involve using the recovered hot water to actually heat ingredients that would eventually be processed in the retorts for a closed loop heat recovery system.
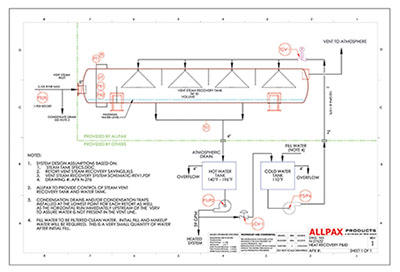
Unique projects with similar drivers
Every revitalization project is unique and yet they each stem from one or more of the core drivers described earlier in this article:
- Demand outstripping capacity
- Growing inability for co-packers to maintain and/or expand the customer base
- Incidental factors such as energy, safety, labor costs, obsolesce, or compliance issues
An interesting side note is that management and operations personnel are overwhelmingly surprised at just how far retorts, retort automation, and retort controls have come when they start diving into a revitalization project. If these companies do not go ahead with revitalization now, personnel definitely file away the possibilities for later. It’s clear that if the drivers were there, each management team would like to jump into a full modernization program.