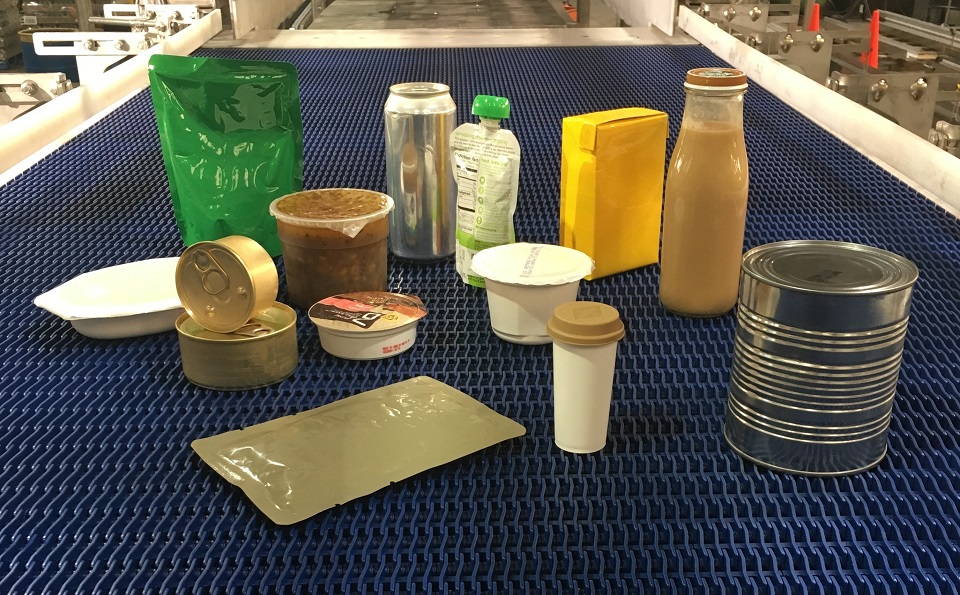
Flexibility – THE Key To Profitable Food Processing
Smaller finished goods inventories, rapid response times, and greater effective throughput are all phrases, among other EBITDA-powered ditties, that have become real pressures on the managers of food processing companies. All of these concepts have to happen if the company is going to be successful in the 21st Century marketplace. And, they have to happen where the rubber meets the road – at the plant.
Certainly, marketing and product development set the bar. But it is the processing line that must deliver consistently and continuously – with high quality results.
Marketing to the World
Companies with a global vision know that what works in the states will not necessarily work in Europe, Asia and emerging countries in the world economy. Products designed to meet the tastes and nuances of the American consumer often need to be changed in many dimensions in order to meet the demands of the new consumer-king in a far-off land.
These changes include product formulation, packaging, and processing parameters. And, it is the company that understands the required processing flexibility – with effective quality and safety controls in place – that will optimize the profits waiting to be made.
Product – Container Flexibility
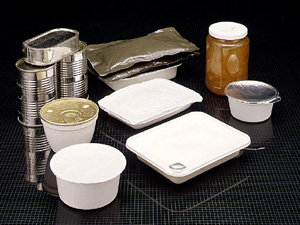
It’s not just cans anymore. In fact every food processing manufacturer – from the multi national brand owners, to the mid sized producer, to the mom and pop “canner” – is looking to optimize their equipment investment by utilizing container flexibility as the cornerstone of their market share and growth plans. The steel can is rapidly becoming the container of the past. Retortable pouches, plastic bowls and bottles, glass bottles and jars, plastic cans, easy open ends, plastic trays and dishes – all with an array of lid stocks and closures – now offer marketing a wide range of options to create new and unique products.
As the marketing programs become production schedules, the demand for plant processing flexibility is obvious. In the past, one product would easily consume the production capacity of a line for weeks, or even months. Today, a long run of a single product / container is no longer the norm. Now, the typical requirement in the modern plant is run – changeover – run – changeover – run. For copackers, this production schedule can take place in one day, once per shift, or several product changeovers each and every shift.
Sterilization Flexibility
Sterilization requirements vary by country – from direct regulatory involvement and oversight in the USA, to a hands-off / “You make it safe” approach in developing countries. Retort processes designed to incorporate significant sterilization safety margins in one country may be modified to take advantage of less stringent requirements in other areas of the world.
The Three Processing Lines of Sterilized Foods
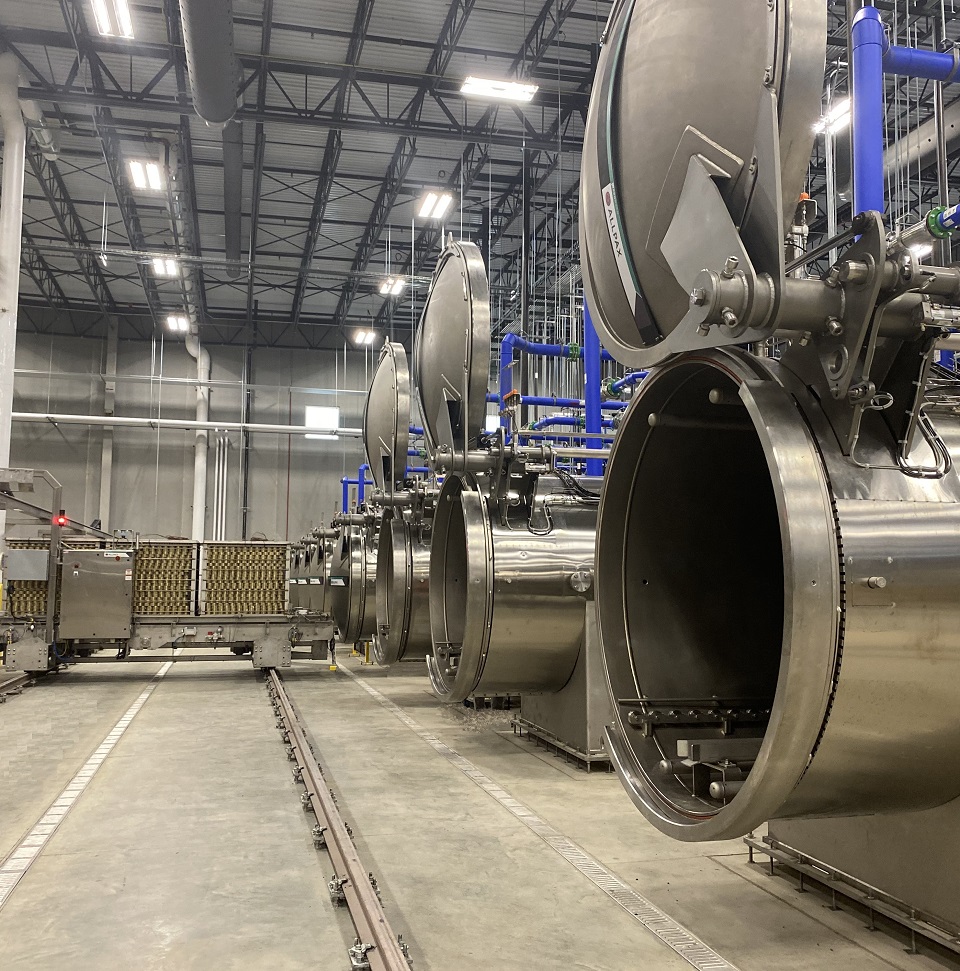
Sterilized food processing lines come in two fundamental flavors: Aseptic lines and In-Container lines, of which there are two types: Continuous, and Batch. Each has their place and their applications.
A quick overview of the three processing line approaches is as follows:
- Aseptic – A sterile container is filled with sterile product in a sterile environment. It is a continuous process. Its applications have been typically limited to liquid products and products with small particulates. Because of its high-capital dollar investment and formulation limitations, most of the products produced with this line are liquid / small particulate, high-margin, value-added products.
- In-Container – An unsterile container is filled and sealed with unsterile product in an unsterile environment. The product is then sterilized inside of the container as it passes through the sterilization processing line. The two types of In-Container sterilization processing lines are:
- 1) Continuous / Hydrostatic – A constant steady flow of product moves into the continuous sterilizer by means of chains (or container guides) and goes through a series of long vertical flights to pre-heat, cook, pressure cool and cool each container before exiting the system. Because of its high-capital dollar investment of a hydrostatic sterilizer and the downtime needed to change from product to product, the application is typically used for high-volume products of a similar container type or size. Also, because of overpressure processing requirements of certain containers, lid stocks, etc., the application is limited to packaging constraints. [Note: There in another type of continuous sterilizer, commonly known as continuous reel cookers, which don’t require the capital investment of a hydrostatic sterilizer. However, these cookers are often subject to the same limitations as the hydrostat. By and large the continuous cookers are considered by many as antiquated technology due to their inability to optimize the process for each product formulation irrespective of line speed. Incremental expansion to meet growing future line speed is not possible (unlike batch retorts).
- 2) Batch Retorts – A constant, steady flow of product moves onto an accumulation table that consolidates the product into baskets. The filled baskets form a train (or batch) of product, and are moved into one of the retort vessels in the bank of retorts. Retorts designed for product flexibility can deliver an array of processes and can handle the full array of product packages.
The Modularity of Batch Retorting
Flexibility is the needed feature in 21st Century food processing and 21st Century technology has made retorting the flexible alternative. Modular sterilization processing give you the options you need to streamline your process.
A Building-Blocks Approach
With an accurately defined requirement, a retorting line can easily be configured to accommodate a wide array of products and containers. The retort vessels, with computer controls that are recipe-driven, will receive and process cans, jars, pouches, bowls, bottles, and trays, in steel, aluminum, glass or plastic, with cap, foil, 3-piece, or EZ open lid stock.
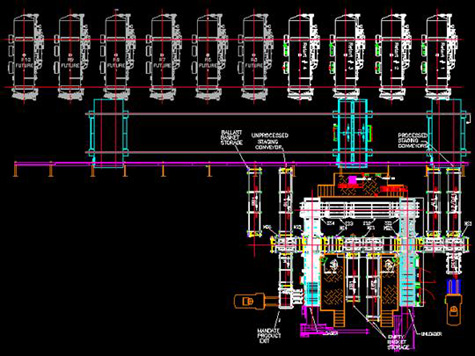
The retorts are configured with the required front-end and back-end consolidating machinery that is specific to the package. A pouch loader/unloader, a can loader/unloader, a tray loader/unloader, etc., are designed to feed into, and pull from, the retort line.
As new containers are introduced, the modular / building-blocks approach accommodates the new loader and unloader, without affecting the processing capability of the line.
As capacity requirements increase, additional retorts are added to the line.
Labor – Automation or Manual
The design of the retort room meets the operational needs of the plant. For world markets where high labor costs drive up the cost per case, automating the basket staging and delivery systems becomes part of the building block approach. ABRS (Automated Batch Retorting Systems) can be operated by as few as 2 operators. Technologies that include basket readers for basket tracking, allow the systems to monitor the sterilization status of each batch of product, and produce digital recordkeeping for quality control and regulatory review.
In Asia and other parts of the world where labor rates are not significant, retort rooms can be configured for manual delivery / push cart approaches, while still using electronic basket tracking for safety and control.
Changeover – Downtime
Flexibility means frequent changeovers to meet production requirements. A properly designed retort room can switch over from one container-product to another in less than one hour! During downtime, the retorts require no changeover and continue to process product from the previous batch, while the loader is being configured for the next container. And, after the last container of the previous batch is being sent downstream to labeling or case packing by the unloader, the retorts are processing the first batch of the next product.
Machine Downtime & Deviations
Because of batch integrity, if a retort drops out due to a mechanical failure, the line keeps running, unlike a stoppage of a continuous sterilization system. Process deviations are easily handled and segregated by batch, and “running out the line,” is not required in order to restart the line. In a batch retorting operation, the line doesn’t stop.
Process Delivery
Product safety is easily controlled by centralizing quality assurance. Recipes that are product-plant specific are controlled and downloaded by corporate quality control, often located in one part of the world, to a plant in a remote country.
Summary
Product marketing is a different ballgame on a global scale. Manufacturing flexibility is critical to allow producers to respond to the ever changing preferences of consumers, their internal marketing teams, or to simply respond to what the competition offers. While options in packaging have given the marketing department an array of product choices, the processing and production of those products have created the need for instant flexibility in the plant. A modular, building-block approach to processing lines can meet these demands today and for years to come.