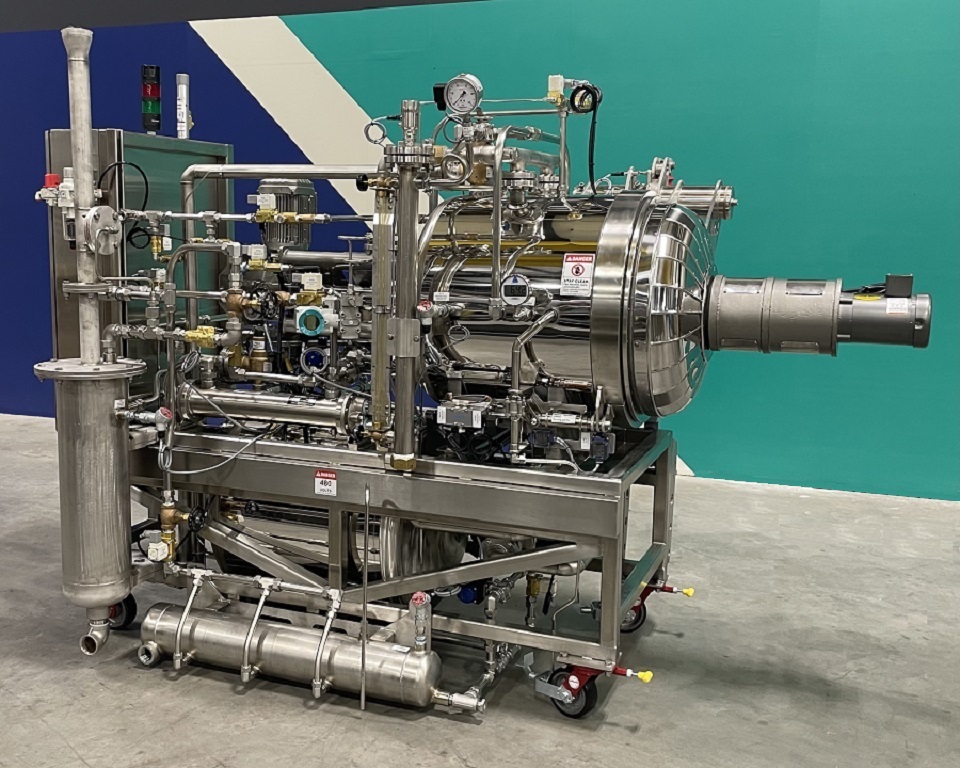
Driving demand
The demand for shelf-stable ready meals is growing for a host of reasons. Changing consumer lifestyles, including longer working hours and multi-schedule households, have led to unstructured meal times. While time-constrained consumers look for convenient, quick-to-prepare meal solutions, they are also demanding healthy, nutritious, and flavorful products. Additionally, changing demographics, including growth in single person households among the workforce and senior population, have expanded the demand for shelf-stable ready meals.
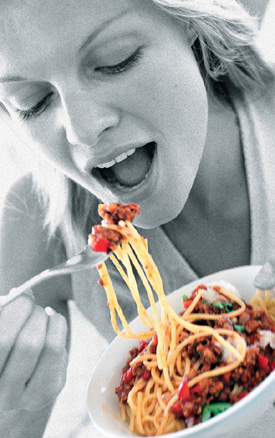
Ready meals have traditionally been sold in rigid packages. With recent advancements in high-barrier film technology and the movement toward packaging that is lighter and puts less material into landfills, brand owners have begun transitioning away from rigid packaging to more cost effective and sustainable film-based flexible packaging for ready meals.
Value-added supplier
As food processors look at their current rigid packaging configurations and attempt to determine the time and cost involved in changing to flexible packaging, they find themselves in unfamiliar territory. With the escalating demand for shelf-stable ready meals, many food processors began asking Amcor Flexibles for insight into the performance characteristics of new retort laminates for pouching and lidding applications as well as how the materials impact the food products’ flavor, texture, appearance, smell, nutritional value, and safety.
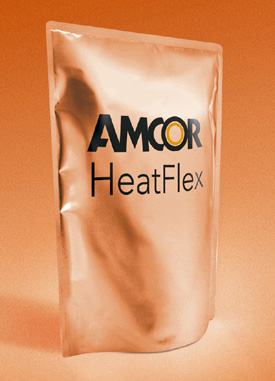
As a worldwide market leader in flexible packaging, Amcor Flexibles has earned a reputation for its broad skill base and comprehensive range of technological capabilities. With its extensive knowledge of retort laminate construction and performance properties of the materials, the company is well known for its ability to help food processors develop optimum retort packaging solutions.
As Amcor Flexibles considered food processors’ time-to-market dilemma, it recognized that the attributes of pouch materials were only one element of the equation. An equally important consideration was the selection of a retort process that would create an end food product that met consumers’ expectations.
While food processors may have commercial style retorts at their facilities, often they were designed for a single, process-specific use. They do not provide the flexibility necessary to test a variety of sterilization processes or offer modes of agitation.
All-in-one retort solution
When Amcor Flexibles learned that Allpax, a division of Pro Mach and a market leader in retort technology, had introduced a new, modular research and development retort with the ability to do saturated steam, steam air, water spray, full immersion, water cascade, partial immersion, and sterilamatic processing, Amcor invested in the retort for its laboratory.
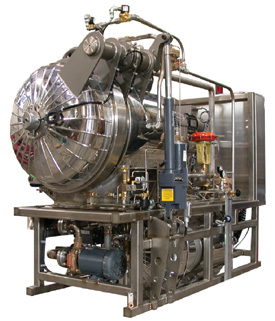
Using the retort, Amcor Flexibles can test and compare the viability of individual processing techniques to help customers quickly develop optimal flexible packaging solutions for shelf-stable ready meals.
Since a retort is a central piece of equipment in a food processors’ facility, installing it in the laboratory enables Amcor Flexibles to emulate the food processor’s process.
The research and development retort and the expertise of the laboratory personnel enable development work to be done outside of a food processor’s facility. This eliminates the loss of production time that would result from dedicating the facility’s commercial equipment for the work. While some food processors have invested in dedicated development equipment, most companies are unable to commit the financial and staff resources necessary.
Using the retort, the Amcor laboratory can quickly and cost effectively research a wider range of solutions and assess which one best meets the customer’s needs. The retort’s sophistication and the laboratory staff’s extensive experience results in processes being defined and optimized, and process boundaries challenged.
Since the retort has the same operator interface and host software packages used with production retorts, food processors are assured of the same operating environment for retorts from laboratory to production. With the all-in-one retort’s onboard human machine interface (HMI), switching between sterilization parameters is fast and easy.
Weeks not months
Using the laboratory retort, Amcor Flexibles can fill a pouch with a food processor’s product, process and test it, presenting a 90 percent complete commercial prototype in a matter of hours.
The food processor can then present the product to its marketing staff so that decisions can be made quickly, enabling a product to reach the market in weeks instead of months.
Time saving supplier synergies
While technological innovations are essential for accelerating food processors’ time to market, creating new supply chain relationships provides a foundation for ongoing time and cost savings.
For information about Amcor Flexibles, contact Franck-Philippe N’Dia, Sales Manager – Ready Meals at 859-368-7762 or visit www.amcor.com. For more information on the new, versatile 2402-FLEX research and development retort, call Allpax at 985-893-9277 or visit www.allpax.com.