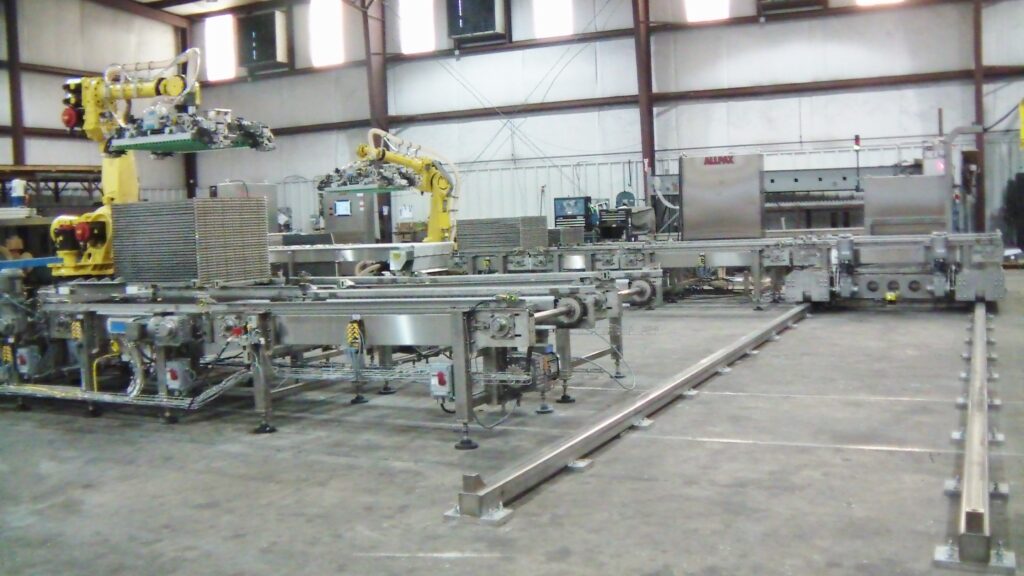
Introduction
There is no doubt that there are advantages to packaging food and beverage products in the retort pouch. Generally, processing times can be reduced by as much as 50% as compared to a comparable sized can, jar, or other cylindrical container. There are also additional advantages which include reduced shipping costs and storage space for the empty containers. The pouch also has good shelf appeal and a growing acceptance by consumers.
There are, however, many processing challenges in using the retortable pouch as compared to a metal can. First and most significant is that a pouch does not fill, seal, or handle like a can. The equipment needed to fill and seal pouches is more sophisticated and expensive as compared to can sealing equipment. The same is true for the handling systems (pouch loaders and unloaders).
The material that follows is an overview which covers those considerations which should be taken into account when planning and designing a retort pouch line.
Major Equipment Components
There are several major equipment categories that comprise a retort pouch line:
- Pouch Filler
- Robotic or Gantry-Type Pouch Loader/Unloader
- Trays that house the pouches that are stacked to become cubes
- Static and Agitated Retorts
- Retort Loading Systems (Drone, Rigid Chain Indexer, Conveyor in Retort, Shuttle, or Manually)
- Case Packer
Allpax Products can supply all but the first and last items.
In designing a pouch line, the desired line speed is what drives most if not all of the other design decisions. For example, the line speed will dictate the type and sometimes the brand of pouch filler/sealer. The filler/sealer will have a characteristic output format for the filled and sealed pouches – single file or “two up”. There is also the strong possibility that there will be more than one filler/sealer in your line.
The piece of equipment immediately downstream to the filler/sealer is the pouch loading station. The loader will have to collate the pouches in a manner that they can be placed in a traying system. Depending on the output of the filler/sealer and the number of filler/sealers in the line, the loader could be presented with pouches in single file, two, four, or more across. The output from the filler/sealer will have direct impact on the design of the loader. More detail on this subject is presented further below.
Tray Design
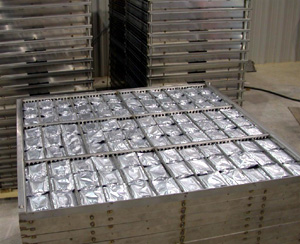
Once the line speed and filler/sealer decisions have been made, tray design considerations are to be made. The layout or pattern of the tray must efficiently work with the robotic pouch loader. The loader will operate most efficiently and at the highest line speed when the number of rows in the tray match or are devisable by the number of rows being output from the filler/sealers.
For example, if there are two filler sealers, each with an output of 2 lanes of pouches, the optimal tray design would be 8 or 12 rows wide (each devisable by 4 which is the total number of lanes being produced. A tray design with 9 rows would not work. It is sometimes necessary to revisit the pouch size at this point, since a small change in the dimensions of the pouch, can sometimes greatly enhance the efficiency of the line design.
Tray racks can be fabricated in one of two ways:
- Metal form stainless steel or aluminum construction
- Injection molded plastic construction
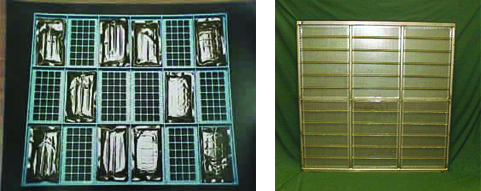
Both the stainless and plastic trays have advantages and disadvantages. Stainless trays have a long service life. They can be produced in small numbers but do have a high individual cost. Injection molded trays typically last about 2 years or more, but are 1/10 the cost of stainless steel. There is however a tooling cost which can be about $100,000. Plastic is also not the best choice once the tray size exceeds 40″ x 40″.
In a basket, cans nest into a pattern and form themselves into rows and columns, separated by a thin divider / slip sheet. Pouches are placed into a tray that must cradle the pouch and protect the integrity of the pouch. It must prevent the weight from other pouches from resting on top of the pouch. The tray, while simple looking, must be well designed. It must be stiff enough for the pouch loader to stack and destack cubes. It must incorporate a design that promotes even temperatue distribution and allow for adequate flow of heating and cooling medium. It must be strong enough to allow for the weight load of a whole cube to be supported by the frame members. It must also be free of any type of burrs or defects that could damage the integrity of the pouch.
Once the line speed, pouch size and tray design are done, it is now time to determine product handling type and capacity.
Handling Pouches
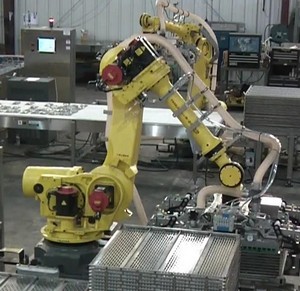
As stated earlier, most design decisions will flow from the line speed definition and the pouch geometry. As compared to cans, line speeds for pouch lines will generally be slower.
The most important aspect in understanding pouch handling is to break any preconceived notion that pouches are similar to cans. Here’s a quote about pouch loading equipment from one of our recent newsletters:
“One of the misconceptions that many folks have regarding pouches is that the pouch can be used with the same material handling system as cans. This is untrue! Pouches behave much differently than cans and require completely different handling techniques. Cans behave like well-trained soldiers that stay organized and move in unison. On the other hand, pouches behave like felines; they go any way they please and are uncooperative.”
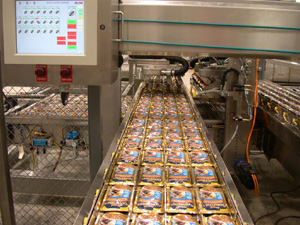
The pouch loader is designed to stage the pouch into a tray pattern – and this must relate to the manner in which the pouch filler feeds them to the loader. Pouches are staged into a tray pattern, then a pneumatic pick and place head lifts the staged pattern and places it into the tray. A fully loaded tray is stacked, one on top of another, to create a cube. The cube is roughly the shape of a retort basket.
Retort / Cube Capacity
Now that the throughput has been determined, additional factors such as process duration and mandate time will allow the manufacturer to determine the size and quantity of retorts needed. One important tradeoff to note when considering pouches is that you won’t get the same quantity of pouches in a retort as you would with cans. Again, due to the nature of cans which nest into overlapping rows and columns. A pouch eats up a lot of room. It must reside in its own compartment. Take a comparative look at capacities in an Allpax Jumbo 6-basket/cube spray retort – example given if for 3 oz can and 85 gram pouch:
- 3oz Cans – 61560
- 85g Pouches (95mm x 125mm x 20mm) – 22032
The Retort Process – Overpressure Retorts
Commercial sterilization of pouches must be accomplished with overpressure – this means that you need air in the retort during the sterilization phases of the process (come-up and cook/hold) as well as the pressure cool step. There are three types of process that you could use to perform an overpressure process. The following describes these process types.
General:
Overpressure retorts are required when sterilizing glass containers, flexible pouches, and semi-rigid plastic containers. They tend to be more complex and expensive than comparable sized steam retorts. Most include pumps, motors, drive units, automated valves, and sophisticated controls. The three types of overpressure retorts which are commonly used include: Full water immersion, Water spray/steam-air, and Forced Steam/Air (with fan). A brief discussion of each follows.
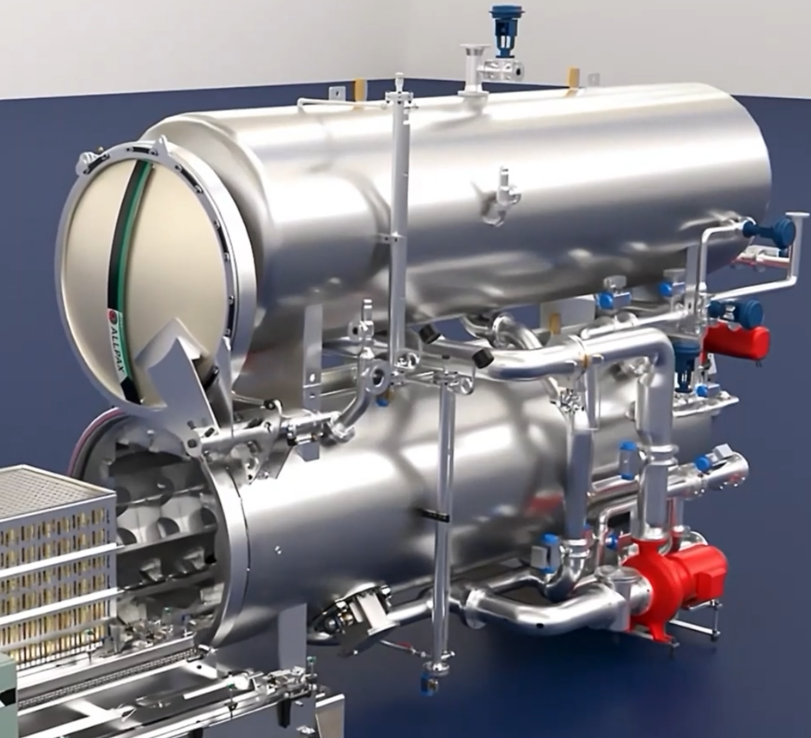
Water immersion retorts generally have the most flexibility when it comes to processing various container types. Water immersion retorts can be effectively run in rotary and non rotary modes. They will process all types of containers and can accommodate containers loaded in “dense pack” configurations (i.e. cans stacked on divider sheets) Full immersion and partial immersion processes can be run providing a wide range of processing flexibility. Steam/Air processes are typically not recommended for glass or for containers which have to be tightly packed. Containers which are loaded in trays which have channels to allow the flow of the steam/air mixture are well suited for this process (i.e. pouches or plastic bottles). Water spray processes are appropriate for most container types but care must be taken regarding container loading patterns. As with steam/air, water spray processes are normally used to process products which are not densely packed. Water spray processes are typically not done in a rotary mode because of the tendency to have the water migrate to the exterior of the basket as rotational speed increases (resulting in poor temperature distribution). Rotary processes are not recommended for either water spray or steam/air because of the non-buoyant environment. A full water process is gentler on both the container and the rotary mechanism of the retort. One alternative for lines that will be used for multiple container types is to consider a Multimode retort. The Allpax Flex line of retorts provides more than one process style in the same retort. This style retort is more complex than a single mode retort, but does provide processing options if more than one container type is to be used. They can be built to order with any combination of process styles. Conventional single mode retorts can be installed in Flex lines that incorporate two or more container handling systems.
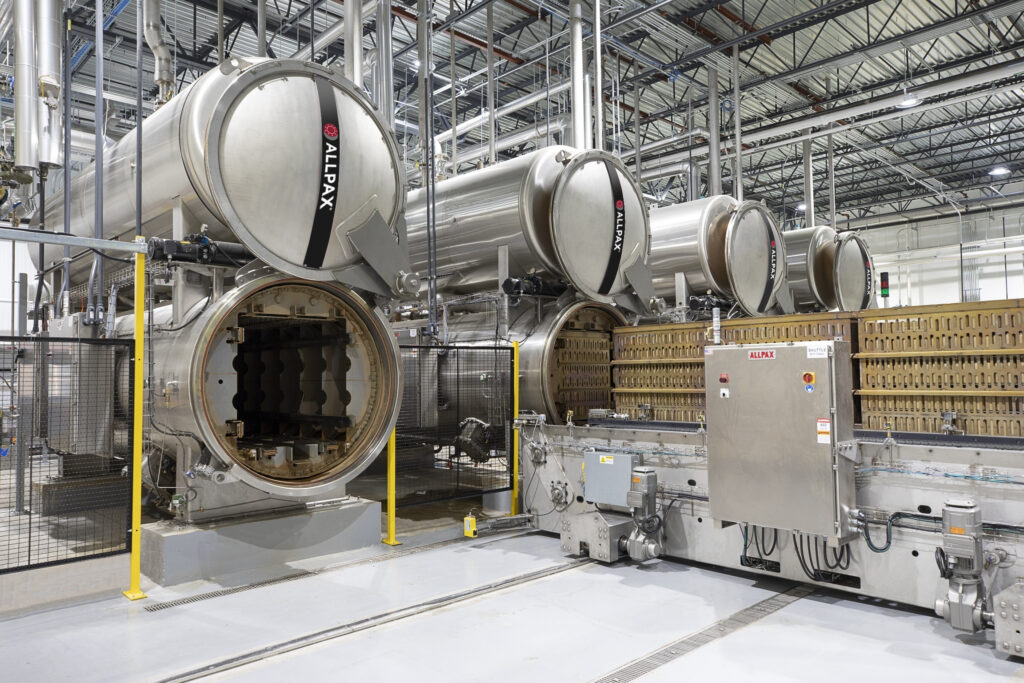
Full water immersion: This style of retort is the most widely used overpressure retort in the industry. Full water immersion retorts are available as either vertical or horizontal versions. The vertical model has historically been used to process glass containers with lug or screw type lids. In this system, water is introduced into the retort at the beginning of the day and brought to a level which will cover the upper most basket when fully loaded.
Once loaded, the temperature and pressure are ramped upward until both temperature and pressure requirements are met. (The pressure setpoint is typically higher than the corresponding vapor pressure attributed to the setpoint temperature). Pressure is maintained during cooling and the cooling water is left in the retort to be used for the next batch. This style of retort in generally not used for new lines.
Horizontal models can be either self contained (with hot well as shown, above) or be single vessel retorts which depend on a centralized hot well. In the self contained models, the retort consists of both a lower processing vessel and an upper storage vessel which serves as the hot well. Superheated water is stored in the upper vessel and dropped to the lower vessel at the beginning of the come-up phase. During the cook phase, pressure is maintained in the lower processing vessel by pressure control in the upper storage vessel. A small amount of water is left in the top vessel and the vessel is pressurized by either steam of air. The pressure is transmitted to the lower drum by a connection valve. Following the cook phase, the hot water is returned to the upper drum and stored for the next cycle. Control pressure is usually maintained until the upper drum is filled and then slowly ramped down. A considerable energy savings is realized since the water which is pumped back only requires a small amount of heating prior the next cycle.
Full water immersion retorts are typically pressure rated to at least 50psi or higher. This style of retort is available in both rotary and non-rotary models. While pouches can be run in full water immersion retorts, other styles of overpressure retorts are better suited for processing pouches. Most water immersion retorts are rotary models which are not needed for pouches.
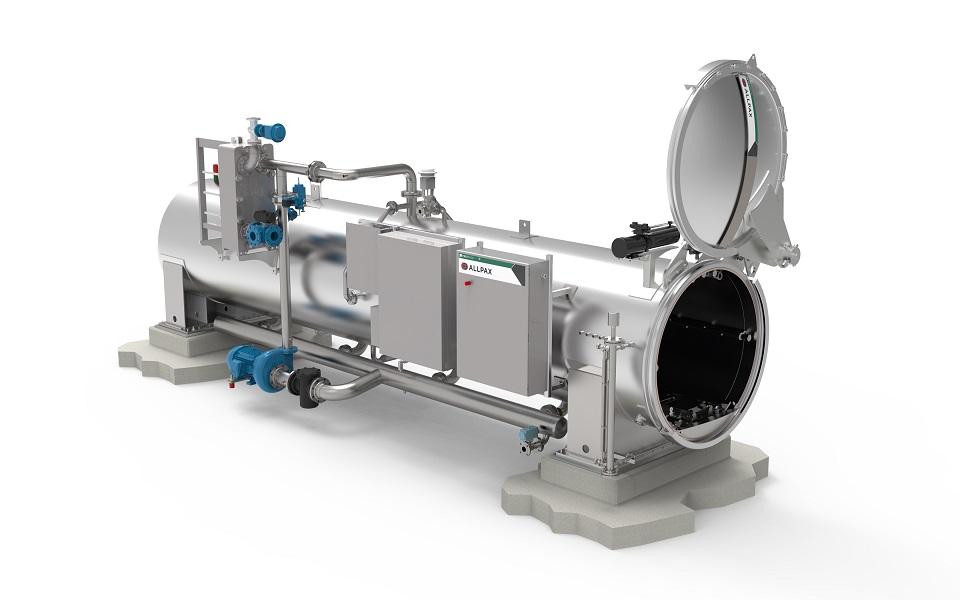
Water Spray: Like the full water immersion variety, the water spray retort is also an overpressure process. Unlike the full water immersion models, the water spray retort uses only a small quantity of water (100-300 gallons) which is pumped at a high flow rate. Water is dispersed by means of a perforated plate distribution system or by spray nozzles. The water is then pumped through a heat exchanger before returning to the distribution manifold.
Models can be built which have an independent storage tank for hot water or no storage tank at all. In the latter model, water is stored in the bottom of the retort. Since the same water is used for both heating and cooling, the use of cooling water sanitizers is eliminated.
Depending on the cooling medium available at the installation site, considerable water savings can also be achieved. Steam is injected directly into the vessel by one or more bottom located spargers. Pressure control is accomplished by air and achieved through a completely independent control loop. Because of the corrosive environment created in this process, it is recommended that vessel construction be of stainless.
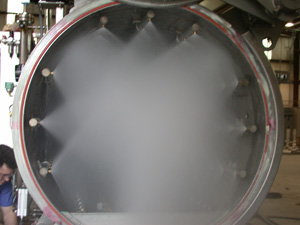
Water spray retorts are typically pressure rated to at least 50psi or higher. This style of retort is available in both rotary and non-rotary models.
Both rotational and non-rotational models are available. Rotary is typically not recommended because of the non-buoyant environment and poor temperature distribution which may be seen at moderate to high rpm’s. Spray processing is a good choice for pouches since rotation is typically not needed.
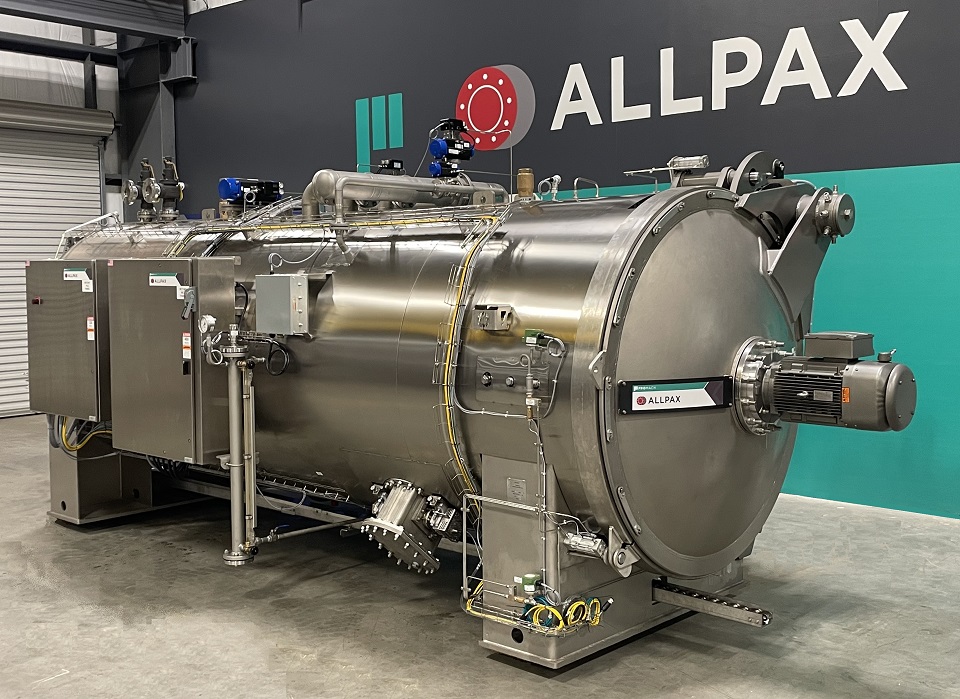
Forced Steam/Air: Steam/Air retorts are the last type of “overpressure” retort. Sterilization in this type of retort is accomplished by using a steam and air mixture which is circulated within the retort by means of a turbine type fan. The homogeneous mixture of steam and air is drawn to the rear of the retort by the fan and then back to the front in a channel between the retort shell and baskets.
As in the spray retort, pressure control is accomplished by air and achieved through a completely independent control loop. Consideration must be given to the desired pressure control setpoint since the ratio of steam and air in the vessel can affect heat transfer. When large amounts of air are mixed with steam to provide overriding pressure, the surface heat transfer coefficients are reduced.
Unlike steam retorts, steam/air retorts require only a minimal vent phase. Steam/Air retorts are typically pressure rated to at least 50psi or higher. This style of retort is available in both rotary and non-rotary models. Rotational models are typically not recommended for glass containers due to the non-buoyant environment. Additionally, dense loads without adequate spaces between containers for the steam/air heating mediun to flow such as vertical nested containers like cans and bottles/jars. While not as commonly used in the U.S. as spray processing, Steam/Air retorts are a good choice for pouches.