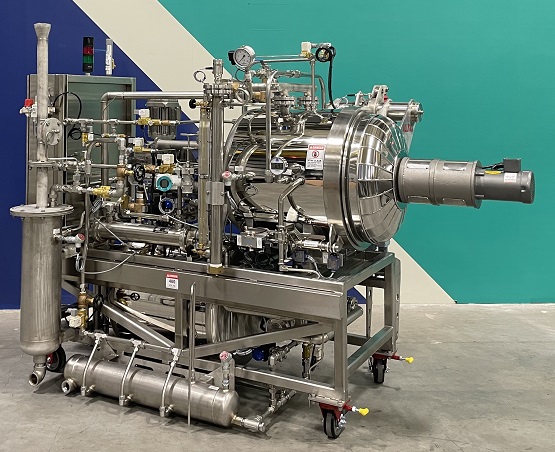
Let’s say it plainly from the start: There is no best retort sterilization process! You heard it right, and this from a leading retort manufacturer. In the same way that we can discount the car salesman who says that his sedan is the best, we can discount the statements of retort vendors who make these absolute claims. A luxury sedan may be best for traveling the open road, or a hybrid car for getting the highest miles per gallon, or achieving some other standard. But, I can tell you, that the luxury sedan, or the hybrid – as good as it is – isn’t what I need to tow my boat. There is no one type (or size) that fits all. It really depends on the application. Retort Sterilization Processes should be evaluated in the same way. Which process is best for the application? And, which process is best for a particular container?
Retorts use steam-based processes. There are 4 steam-based processes that are used in sterilizing food, nutraceutical and pharmaceutical products. Steam can be the direct heating media (for example, saturated steam) or the indirect heating media (steam-heated water used in a water immersion process). The types of retort processes are:
- Saturated Steam – direct steam heating
- Water Immersion (Rotary and Static) – indirect steam heating
- Water Spray (Rotary and Static) [Note – Cascading Water is also included in this type] – indirect steam heating
- Steam-Air (Rotary and Static) – direct steam heating
As in all forms of design and engineering, each of the processes have pluses and minuses. Each has tradeoffs, and it is the objective of this paper to generally define the process, then explain these tradeoffs. For information on a detailed step-by-step description of each process, please refer to: Understanding the Retort Processes, a white paper for each process that can be found on this web site.
Saturated Steam Retorting Process
Trade Offs Using the Saturated Steam Process
Pros | Cons |
Low Capital investment, particularly with carbon steel retorts | Venting uses a lot of steam and is not an economical step. Uses a lot of energy. |
Easy to operate manually | Inflexible – typically limited to processing heavy sidewall containers, such as cans. |
Can process most canned product | Cannot process most fragile containers, such as pouches, plastic bottles and plastic jars. |
While overpressure process retorts are gaining in popularity due to the introduction of new types of containers requiring overpressure sterilization, the old, steam retort is hard to beat for its low capital investment, along with its simplicity of design and operation. If you have a limited capital budget and your current and future product mix is limited to cans, then Saturated Steam retorts may be your best decision.
The Water Immersion Retort
(Static or Rotary)
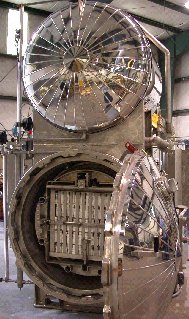
The Water Immersion Process is the most widely accepted method of sterilizing product using an overpressure process. The Water Immersion process is similar to a saturated steam process in that the product is totally isolated from any influence of cooling air – the product is totally submerged in water. But, it is different from Saturated Steam in that air can be introduced into the vessel during sterilization. Overpressure is provided by introducing air (or steam) on top of the water. In some instances, air is added to the steam (which then heats the air). The heated air agitates the water as it flows to the surface and serves to pressurize the process load.
The Water Immersion retort is flexible in its operation. Because it is an overpressure process, the machine can handle most, if not all of the fragile containers.
Trade Offs Using the Water Immersion Process
Pros | Cons |
Can utilize carbon steel vessels – although Allpax recommends Stainless Steel for all overpressure processes. | Higher Capital Investment – if a double (piggy-back style configuration) tank system is used. |
Flexible – can process virtually all types of containers | Virtually impossible to operate manually, given the complexity of piping. |
Excellent application for rotary processes due to buoyancy of the load in a full water immersion process. | Machines with rotary processes require significantly more maintenance time and money. |
Can provide for a partial immersion process with a rotary configuration. | |
Best application for rotary processes in excess of 10 RPM’s. | |
The storage tank allows for energy savings by capturing process water after sterilization – particularly in the energy savings mode |
The Water Immersion retort had, at one time, taken a secondary position in popularity to the other types of overpressure retorts. However, in recent years, this machine has mounted a strong comeback in popularity – particularly for products that need a rotary process. While the initial investment is steeper than the other retorts, it is the machine for rotary processes.
The Water Spray Retort
(Static, Horizintal Reciprocation or Rotary)
The Saturated Steam Process is the oldest method of in-container sterilization. Since air is considered an insulating medium, saturating the retort vessel with steam is a requirement of the process. It is inherent in the process that all air be evacuated from the retort by flooding the vessel with steam and allowing the air to escape through vent valves. There is no overpressure during the sterilization phases of this process, since air is not permitted to enter the vessel at any time during any sterilization step. However, there may be air-overpressure applied during the cooling steps to prevent container deformation.
The Water Spray process is also an overpressure process, like water immersion, except that the product is exposed to the influence of the overpressure air. It is similar to the Saturated Steam process in that steam is the driving force for reaching the center of the load. But, the Water Spray process is different from Saturated Steam in that air can be introduced into the vessel during sterilization. Overpressure is provided by introducing air (or steam) into the retort. To overcome the insulating effects of the air, the spray nozzles vaporize the steam and mix the steam with the air. Some Water Spray retorts are manufactured with a rotary option.
The Water Spray retort is flexible in its operation. Because it is an overpressure process, the machine can handle most, if not all of the fragile containers.
Trade Offs Using the Water Spray Process
Pros | Cons |
Typically a lower capital investment – compared to the other types of overpressure retorts | Is generally not a good option for rotary processes – particularly for those that exceed 10 RPM’s |
Flexible – can process virtually all types of containers | Machines with rotary processes require significantly more maintenance time and money. |
Energy efficient – utilizes a heat exchanger and pump to recirculate both sterilizing water and cooling water. | Come Up times are typically longer for high RPM rotary processes. |
Sterilizing / cooling water can be reused without chemical treatment for the next process. | Cooling times may be extended due to indirect cooling (via heat exchanger) and for tightly packed product where spray cooling is used. |
When configured with a storage tank – The storage tank allows for energy savings by capturing process water after sterilization. |
The Water Spray retort has become one of the most popular in the USA, primarily because it has the best ratio of flexibility to the investment required. The machines are relatively simple in design for an overpressure process, and are a good buy for static processes. Low RPM rotary processes are also acceptable in this machine, adding to its flexibility. (It should be noted that processes in excess of 10 RPM’s may experience increased “Come Up Times,” due to thermal distribution difficulties that may be inherent in the machine’s design.
The Steam-Air Retort
(Static or Rotary)
The Steam-Air process is an overpressure process, like water immersion, except that the product is exposed to the influence of the overpressure air. Because overpressure air enters the retort with steam, and steam is the only heating medium, a large fan is used as a driving force to mix the steam with the air, to prevent cold spots in the machine. The fan is used in conjunction with a baffling arrangement inside of the retort to channel the heated steam-air mix to the center of the retort load.
Some Steam-Air retorts are manufactured with a rotary option. The Steam-Air retort is flexible in its operation. Because it is an overpressure process, the machine can handle most, if not all of the fragile containers.
Trade Offs Using the Steam-Air Process
Pros | Cons |
Typically a moderate capital investment – compared to Water Immersion retorts | Is generally not a good option for high-RPM rotary processes – particularly for those that exceed 15 RPM’s |
Flexible – can process virtually all types of containers | Machines with rotary processes require significantly more maintenance time and money. |
Energy efficient – utilizes a fan for forced convection. | The Fan is a moving part that adds to the complexity / maintenance of the retort that is unique to the Steam-Air process. |
Other than the addition of the fan, the machine is a generally simple design and an easy process to administer. |