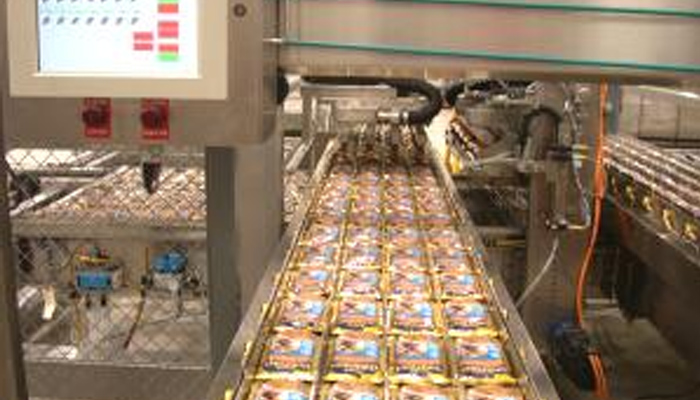
You’ve just been told that marketing has decided to launch a new product – in a pouch, or plastic bowl, or plastic bottle – and that the container must go through the rigors of the retorting process. You’ve been given the project and the burden is on your shoulders to make the project a success. You’ve got to find the keys to make the product at the line speeds needed to supply the marketing projections. After the shock of the announcement has subsided, the mind starts to work – “What does this mean?” “What do I do?” “Where do I begin?”
What does it mean? Well, it means that you have to identify the technology that is needed to make your project successful. The good news is that there is no new technology needed to pull it off! All of the equipment and processes that you need to provide you with a successful project have already been developed. Sure, it may take a variation or derivation of an existing machine to meet your packaging requirements. Every marketing department wants a unique, signature package that sets their product apart. Unfortunately, this decision never takes into account the machinery design and process ramifications. Most marketing types simply say, “that’s just a small design detail that needs to be worked out!” Well, again, the good news is that it can be worked out.
In the Retort Room only… This paper addresses the machinery and processes needed in the retort room to sterilize the product in the container specified by marketing. There will be a number of decisions to be made when planning for a project of this magnitude, but this paper will attempt to address the key retort-room-only decisions. Equipment up-stream of the retort room, such as batchers, mixers, fillers and cappers / seamers, will not be addressed, as well as machinery and processes down-stream from the retort room, including labeling equipment and case packers. But, when it comes to the retort room, here are the key questions to start with:
1. Can I use my retorts?
The question is not whether your retorts are too old, or too small (although capacity may be an issue). The real issue is the type of process that your current retorts deliver and the amount of control that the operator has over the process. Pouches and most retortable plastic containers require what is known as an overpressure sterilization process. If your company produces canned product, most likely you are using a saturated steam process to sterilize the product. Don’t get confused with the term “overpressure,” in your process. Most saturated steam processes have overpressure cooling capability – but this is very different from overpressure sterilization.
Saturated steam sterilization requires that all air be eliminated from the retort before sterilization can begin. Overpressure sterilization means that air is actually introduced into the retort during sterilization, as a means of adding pressure around the outside of the containers to prevent container deformation. As thin-walled containers (such as pouches) begin to heat and mix with the gases inside of the container, the internal container pressure increases at an increasing rate. Without sufficient external pressure, greater than that supplied by steam alone, the container will deform or rupture. Hence, we see the need for an overpressure sterilization process.
2. Does your retort line have an overpressure sterilization process?
Use the simple table below to determine if your retorts can deliver this process:
Retort Process | Overpressure? |
Saturated Steam | No |
Water Immersion | Yes |
Water Spray | Yes |
Cascading Water | Yes |
Steam-Air | Yes |
Well, this is the start of your journey in evaluating retorts. If you cannot use your existing retort line, now is the time to get a retort manufacturer involved to work with you to identify the best retorting process for your product. If you can use your retorts, material handling issues and concerns are next in line, with the key question having to do with the way that the containers are consolidated for retorting.
3. Are the containers stackable?
(or, Can I use my existing loaders and unloaders?) Again, using cans as a basis, in order for the product to enter the retort, the cans must be consolidated into retort baskets or trays (which are stacked to form a cube the same size and height as a retort basket). This is achieved by feeding the containers to the basket / tray loader, which stacks the cans in layers, using a slip sheet (or divider sheet) between the layers to even the weight distribution and make the cans easier to load and unload.
Because retortable plastic bottles, bowls and products packaged into pouches are often considered to be fragile containers, special racking systems are needed to support the container, and to support the layers of containers on top of the bottom layers in the basket or cube.
Design of the racking system is critical from a couple of perspectives. First, the rack must have the structure and strength to support the weight of the containers inside of the rack, and then, from the bottom of the stack to the top. Second, the rack must be designed to handle the line speed requirements of the loader. Third, the rack must allow for adequate sterilization process flow to provide for even temperature distribution in the retort during sterilization and cooling.
4. Will I need automation to achieve the line speeds?
After all is said and done, this question may be the question that drives the decision on new retorts. Another way to ask the question is, “Can my retorts and material handling system meet the new line speeds?” In most cases, the answer leads the engineer to new retort room machinery. High line speed requirements, with overpressure sterilization requirements, with racking and special material handling needs often dictates the direction of the decision. When this is the case, large capacity retorts, combined with a fully automated loader and unloader is often the answer.
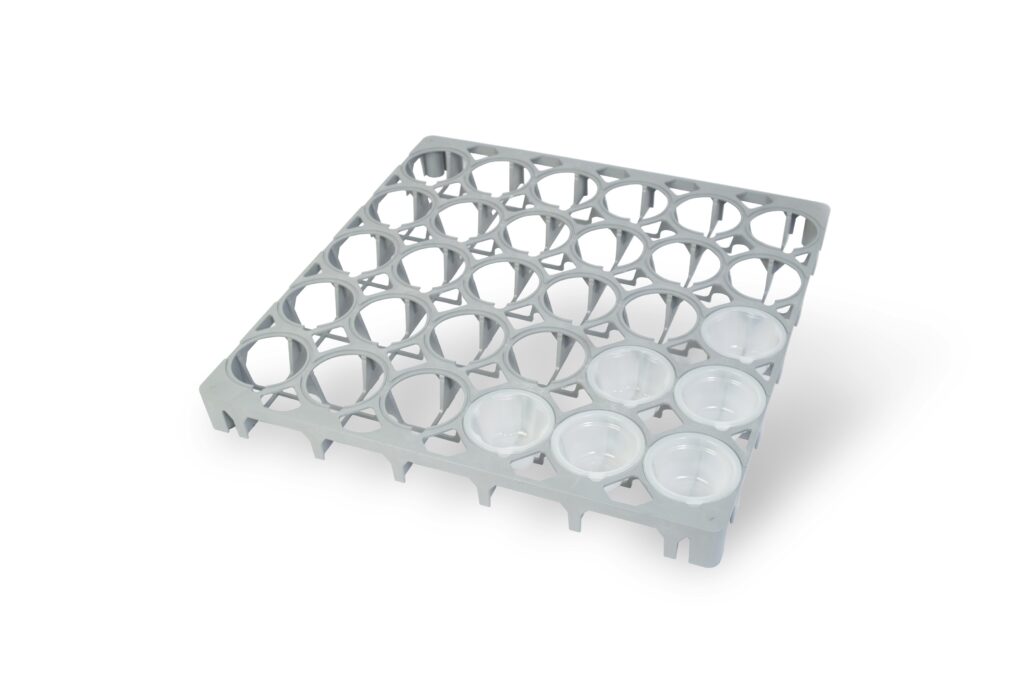
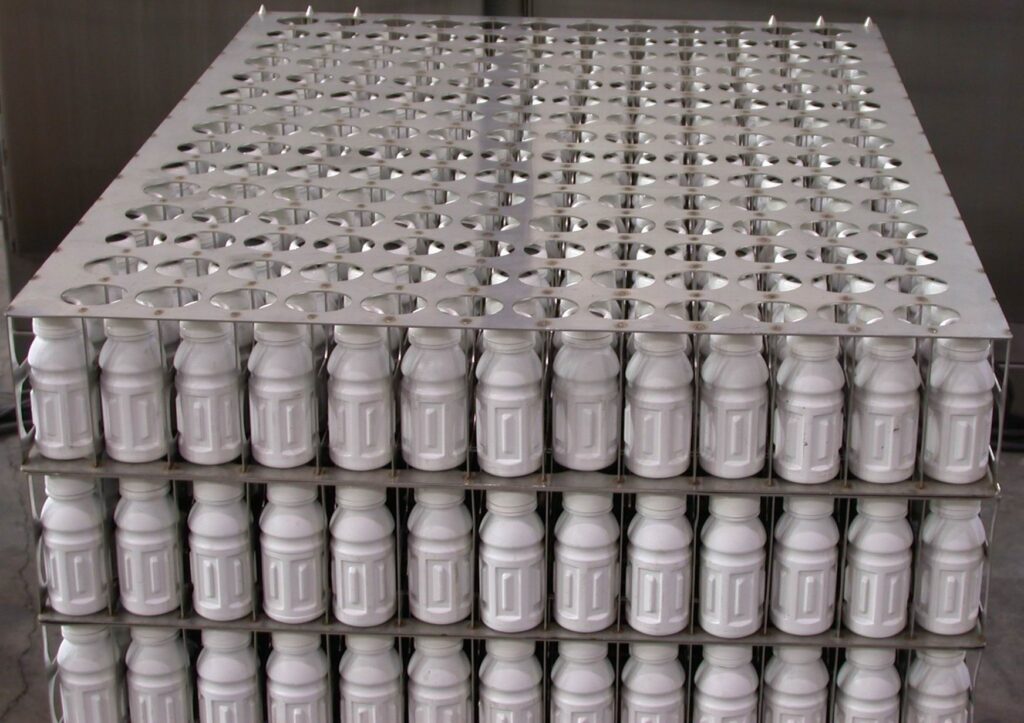
5. What’s next?
These few questions and obstacles are just the beginning. But, the good news is this: your project is likely not virgin territory. Someone has already solved most of the problems that you see (as well as some that you may not have seen.) It’s time to get the players involved, and these players will likely include consultants (people who have done this before), vendors (again, people who have done this before), and your project team. Together, you will identify common obstacles as well as those that are pertinent to your company, your plant, your container, or your project. And, together, you will overcome those obstacles and be on your way to a successful project.