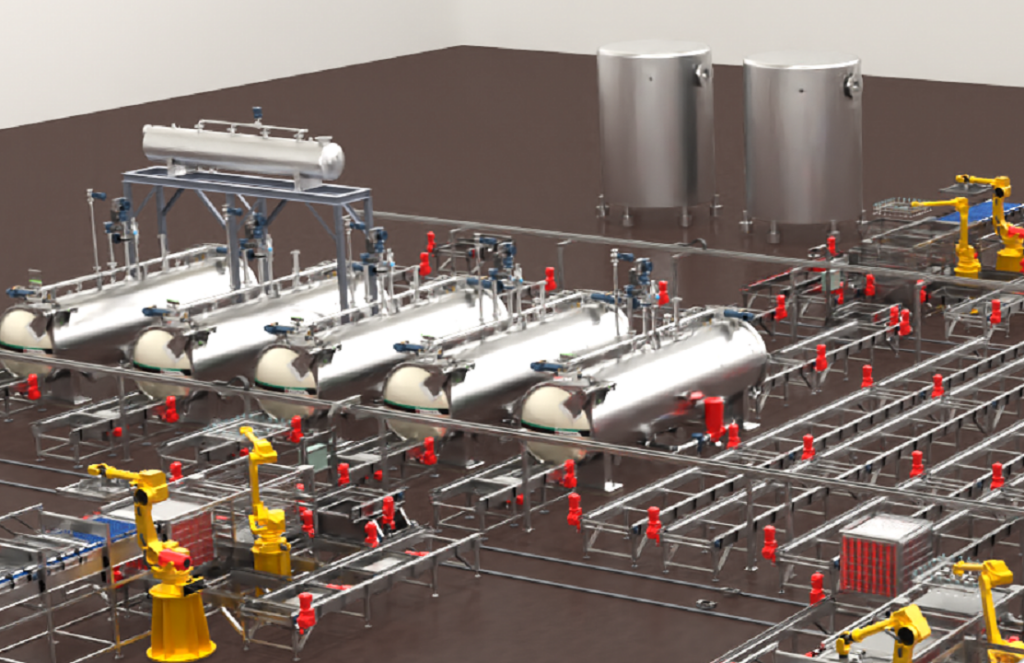
Sustainability has become more than just a buzzword. The effects of a growing global population tax our limited resources. In the modern age of food manufacturing, it’s not enough to just run a clean operation. New efforts are needed to reduce and/or reuse the resources currently employed.
Additionally, new governmental regulations and natural market evolution pressure manufacturers more than ever to improve on sustainability and efficiency issues and challenges.
Though batch retort processing is not a new technology, Allpax has developed innovative ways to minimize the consumption of resources through methods of reusing and recovering the large amounts of water and heat energy expended in an industrial commercial retorting operation. Increasing efficiency involves optimizing retort designs and processes while reducing resource usage, all while producing safer and higher quality products.
Allpax has been focusing on delivering sustainability solutions to the food manufacturing industry by employing one or both of these types of systems:
- Vented Steam Heat Recovery (VSHR) Systems for saturated steam retorts
- Cooling Water Recovery Systems for any type of retort operation
Vented Steam Heat Recovery Systems
Saturated steam retort processing is a common, and also the oldest, method of thermally processing shelf stable products containerized in steel cans or other types of rigid containers. This process involves a vent step where air is purged out of the retort using a large volume of steam. Allpax developed a method of recapturing the vented steam vapor, which is normally just expelled into the atmosphere, and condensing it to be able to re-use the entrained thermal energy. A specially designed chamber/tank is employed to capture the steam vapor without creating any backpressure on the vent line. The zero backpressure on the vent line is an FDA requirement. In the chamber, a fine mist of water collapses the steam and creates hot water in the process. The hot water can then be used, directly or indirectly, for other needs in the plant such as cleaning water, heating product, or heating boiler feedwater. Up to 150 to 200 gallons per minute (GPM) of hot water can be generated from a large steam retort during the vent open phase of each process cycle. With systems comprised of multiple retorts, and with each of those retorts running many cycles per day, a significant amount of heat energy can be recaptured and used.
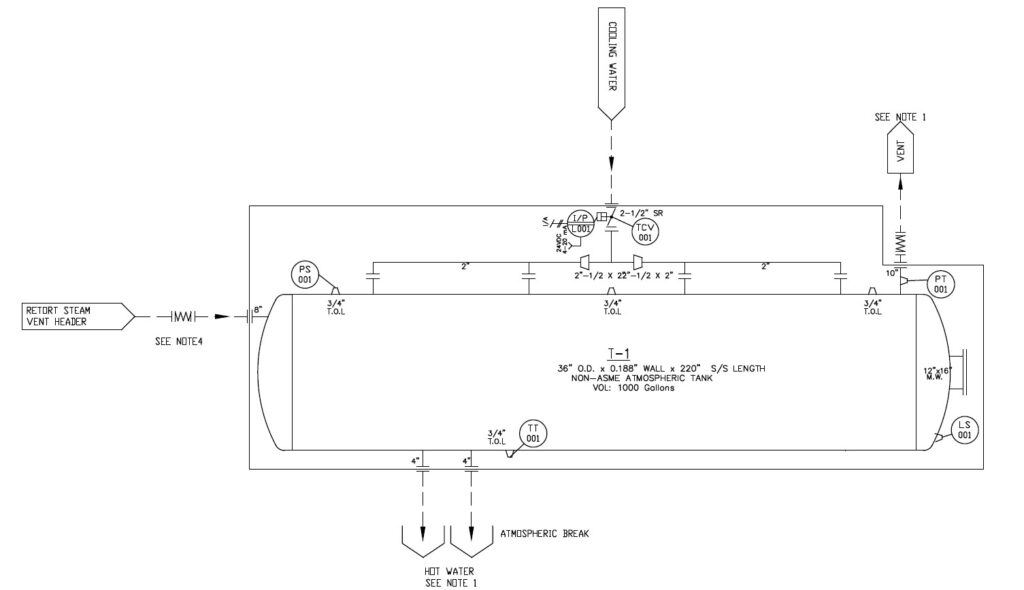
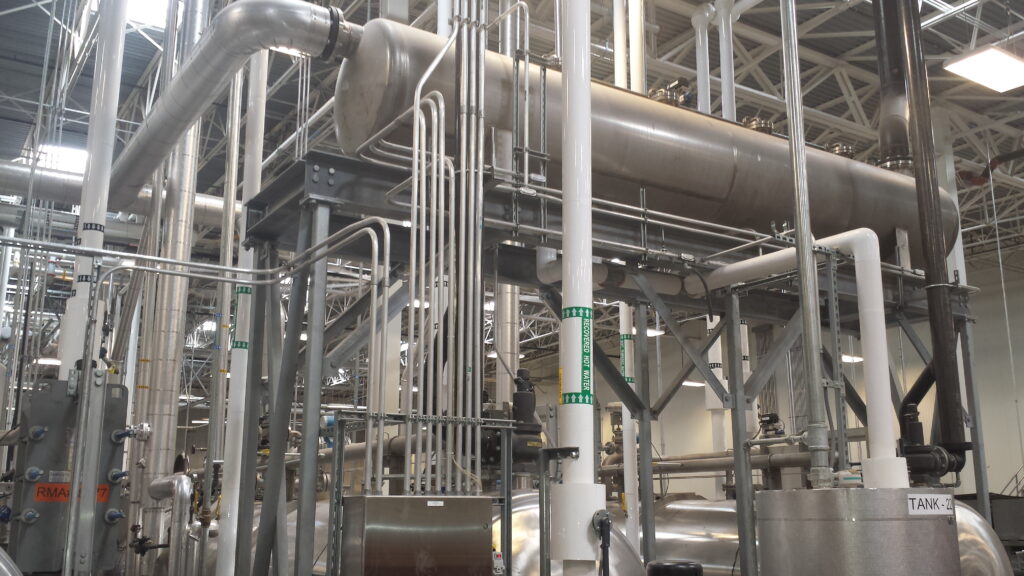
The above diagram and image depict a vented steam heat recovery system operating at a large retort processing facility. The system, which receives vented steam from four 60-inch diameter, 6-basket saturated steam retorts, produces over 8.7 million gallons of 180°F hot water per year. This reduces the manufacturer’s annual reliance resources by more than 2.6 million kilowatt-hours (kWh) of electricity and more than 9 million cubic feet (MMf³) of natural gas. The reduction in energy consumption afforded by the heat recovery system reduces the plant’s carbon footprint by more than 1.1 million pounds of carbon dioxide (CO₂) per year.
Cooling Water Recovery Systems
All methods of batch retort processing employ steps for cooling the containerized products down to a safe temperature after sterilization. A large volume of water either directly (flooded, single pass) or indirectly (through a heat exchanger) is used to cool products down as quickly as possible. Allpax developed several types of water recovery systems to capture and re-use the coolest (i.e.: <140 to 150ºF) discharged cooling water outflow for subsequent retort cooling cycles, and/or to extract the heat energy out of the hottest (i.e.: >150ºF) cooling water outflow for other needs in the plant, such as cleaning water, heating product, or heating boiler feedwater. In a steam retort with direct cooling, up to 50% water savings can be achieved by reusing cooling water from a previous retort cycle.
In the case of a rotary water immersion retort process, at the very beginning stages of the cooling step (pressure cool) the superheated water in the process vessel is recovered by pumping it back into the preheat storage vessel. That hot water is then reused in the next retort process cycle, thus saving a significant amount of water and British Thermal Units (BTUs) each batch. For the remainder of the cooling cycle, the cooler (and clean) discharged water can be stored or recirculated through a cooling tower and/or chiller and can be re-used for a subsequent retort cooling cycle.
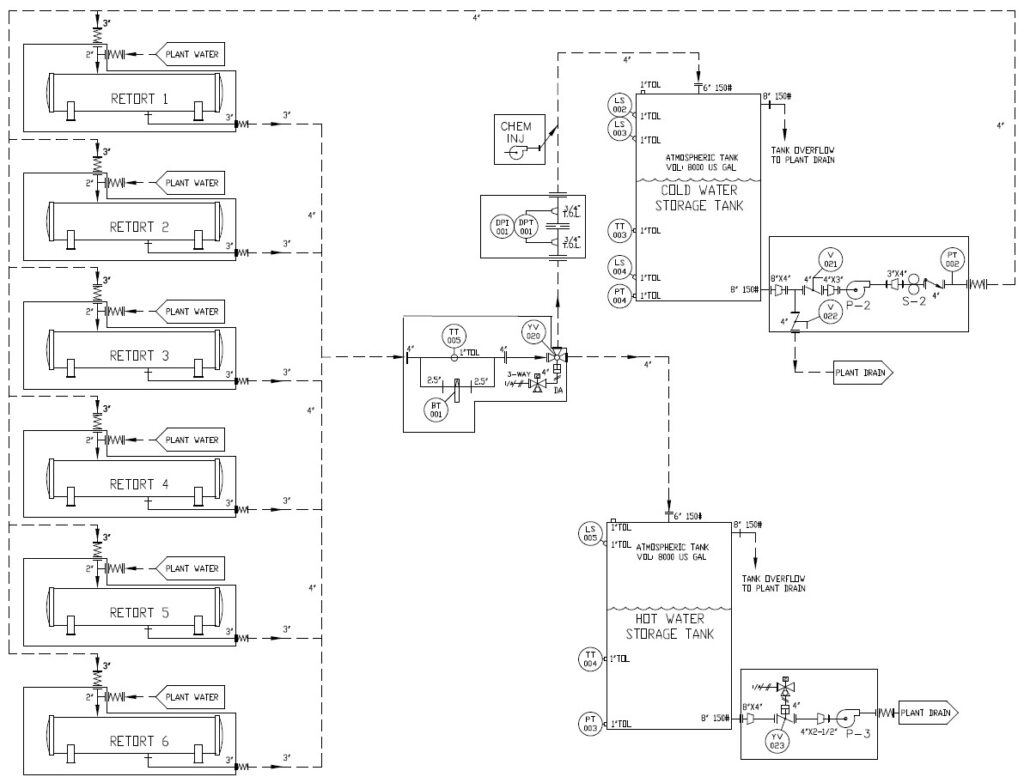
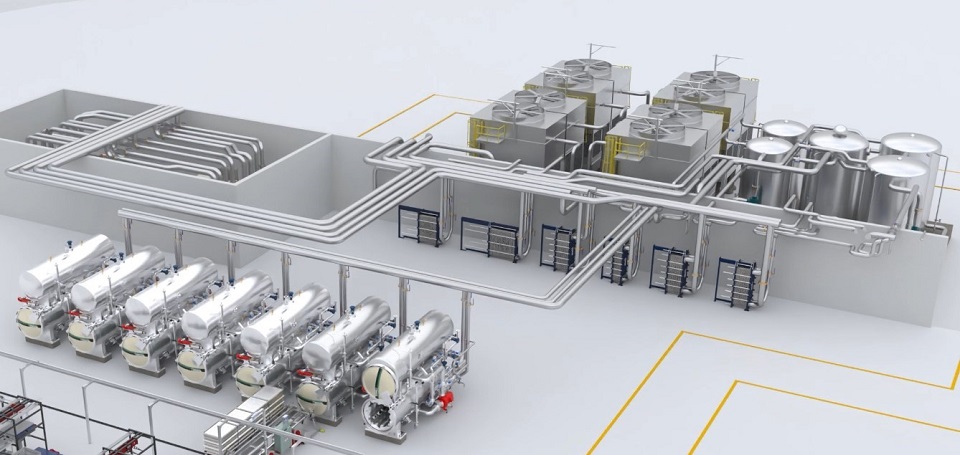
In one example, a Cooling Water Recovery system services two side by side automated batch retort systems consisting of 14, 1800mm (72”) diameter, 6-basket retorts. The system recovers and reuses on average 4.4 million gallons of water every month, water which would otherwise be discarded as waste into the city’s sewer system. The reduction in water usage saves the operator approximately $50,000 per month in water supply and sewer disposal costs.
While larger food manufacturers are currently employing these types of resource recovery systems, in some form, it is becoming a viable option for smaller manufacturers as well. Regional water scarcity and rising energy costs drive the need for efficiency improvements, giving these systems an attractive return on investment for all business sizes. The global market is increasingly more environmentally conscious and demands companies to respond. These systems provide food manufacturers with viable and practical methods to reduce their reliance on natural resources and thus their impact on the environment.